Sheet metal fabrication is a process that involves cutting, bending, punching, welding any many other possible steps depending on the part design. The result would be a part that achieves its desired shape and geometry — but it is not quite the finished product. At this point, the unpolished part would be riddled with machine marks, burrs and other stains from the rigours of the previous steps, appearing crude and unappealing. Hence, this is where the finishing step comes in!
Purpose of Surface Finishing
Finishing is most commonly done for aesthetic reasons, especially for parts that are to be sold to consumer markets later on. Another important reason is the protection of the part itself from the many types of wear and degradation, including corrosion, chemical and mechanical natures. Other reasons can include surface friction or adhesiveness, which may demand rougher finishing. In essence, the application of the part is the most important in determining the type of finishing required, whereas the raw unfinished part rarely sufficiently satisfies any kind of engineering application.
Common Types of Finishing
- Anodizing
- Brushing
- Plating
- Polishing
- Powder Coating
- Sandblasting
Anodizing
This process is usually specific to aluminum parts as it involves the formation of protective aluminum oxide. The aluminum part is submerged into an acidic bath, with electricity being passed through the solution and the part serving as the anode. The oxygen released at the anode later forms the aluminum oxide layer on the surface of the part. Other than the resistance from corrosion, the protective layer also allows for any dye to be absorbed into its porous structure, providing many options for decorative finishing. Another interesting property is the insulation of the part from electricity, which makes this finishing ideal for many applications, including those exposed to weather.
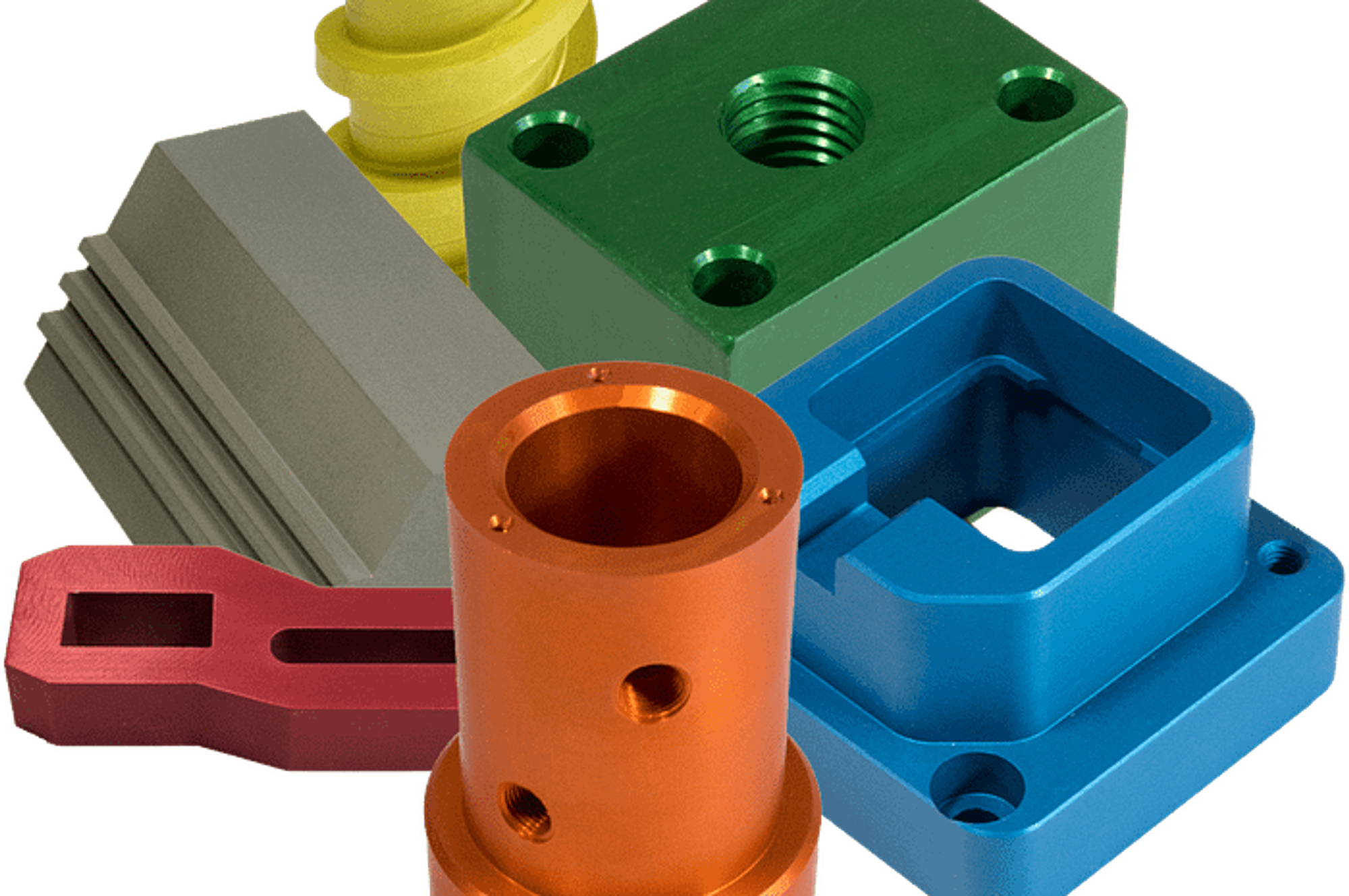
Brushing
As the name suggests, this process employs an abrasive brush typically made of steel wires or other fibers, which is spun at high speeds constituting the brushing action. It is able to effectively remove burrs, but at the same time limits its effect on a single edge of the part, preventing unnecessary brushing of other surfaces. Brushes can also round down sharp corners created by adjacent surfaces, which again in the process, does not affect the material on the surfaces itself. Lastly, brushes can also clean surfaces of the part, removing marks and dirt. As a whole, the finished product is clean, smooth and most importantly, with all its dimensions and tolerances intact.
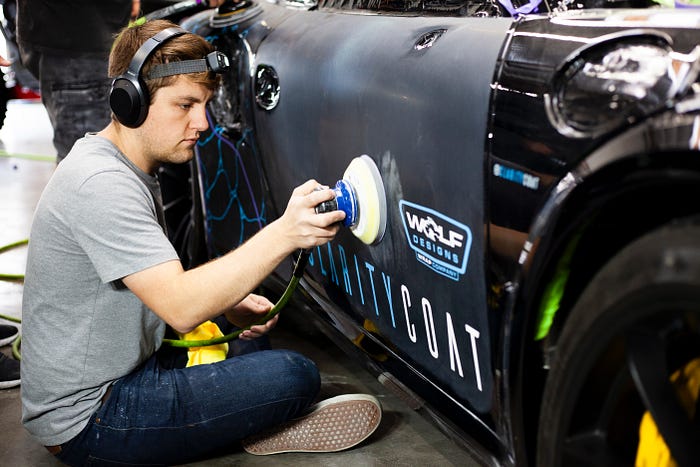
Plating
This process involves a part submerged in a solution containing the ions of the desired metal used for plating, which can be done with or without the use of electricity. With electricity, electroplating enables greater control over the plating process when the electrical current and concentration of ions are adjusted, especially in the thickness of the plating layer and the speed of the chemical reactions. Without electricity, autocatalytic plating is achieved when the chemicals in the solution are unstable, depositing metal onto the part — which does not need to be conductive, unlike electroplating. Electroless nickel plating is an example of a popular method of plating because of the higher corrosion resistance over using chrome which in itself already has good corrosion resistance.
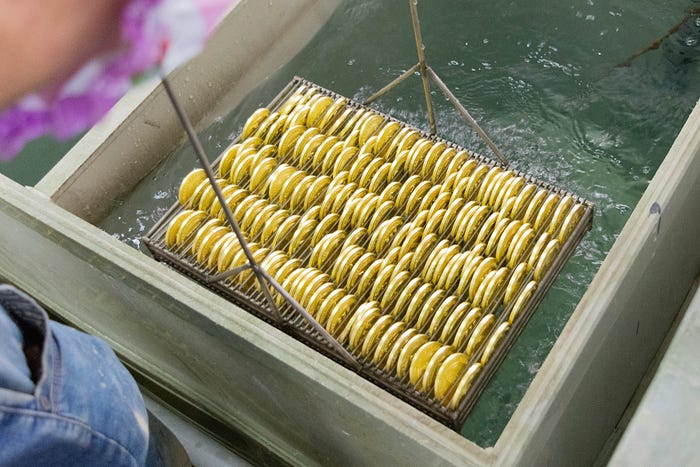
Polishing
Similar to brushing, this process uses abrasives in its tools. However, the abrasives here are much finer, usually in the scale of microns. Hence, this step is usually carried out after rougher processes such as brushing, removing much less material than the steps prior. Ultimately, a previously dull finish will be replaced by a gleaming reflective finish, greatly increasing its aesthetic appeal. Besides the appearance, the polishing step also increases corrosion resistance since uneven surfaces, which are more prone to oxidation and corrosion, are reduced significantly.
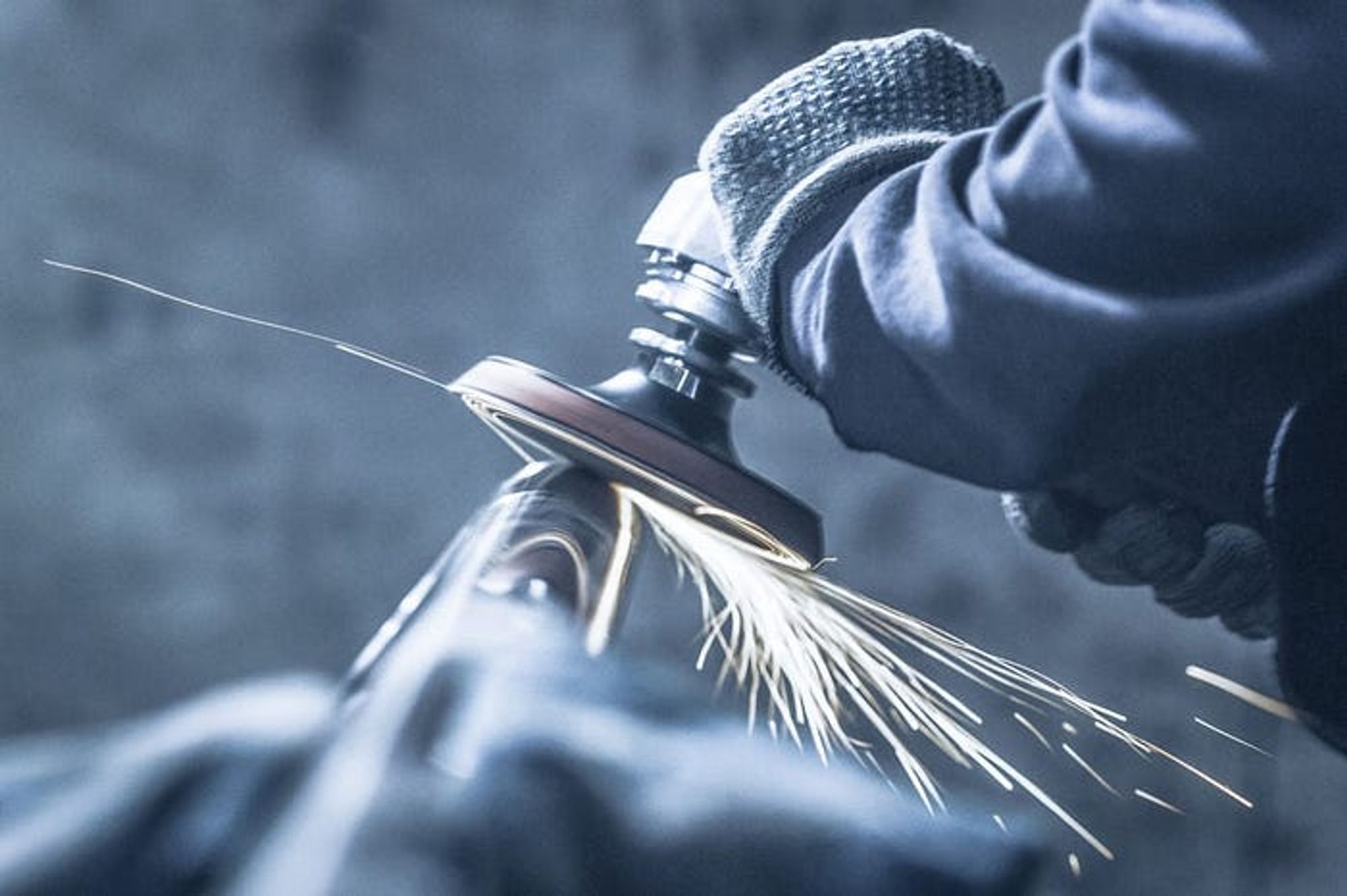
Powder Coating
Powder coating is achieved through the use of a spray gun which charges the powder as they leave the spray nozzle. Since the workpiece has to be able to hold electrostatic charges required to adhere the powder, the most common materials to powder coat are metals such as different types of steel. The opposite charges between the powder and the grounded workpiece ensures even adhesion. The coated workpiece is then heated in the oven for the powder to cure, strengthening the bonding within the coating. Should thicker coatings be needed, this process can be repeated further. A major advantage of a coating is the physical barrier it acts between the inner workpiece and corrosive substances. Another plus is the wide range of colours available for coating, unlike plating which is restricted to the natural colour of the plating metal.
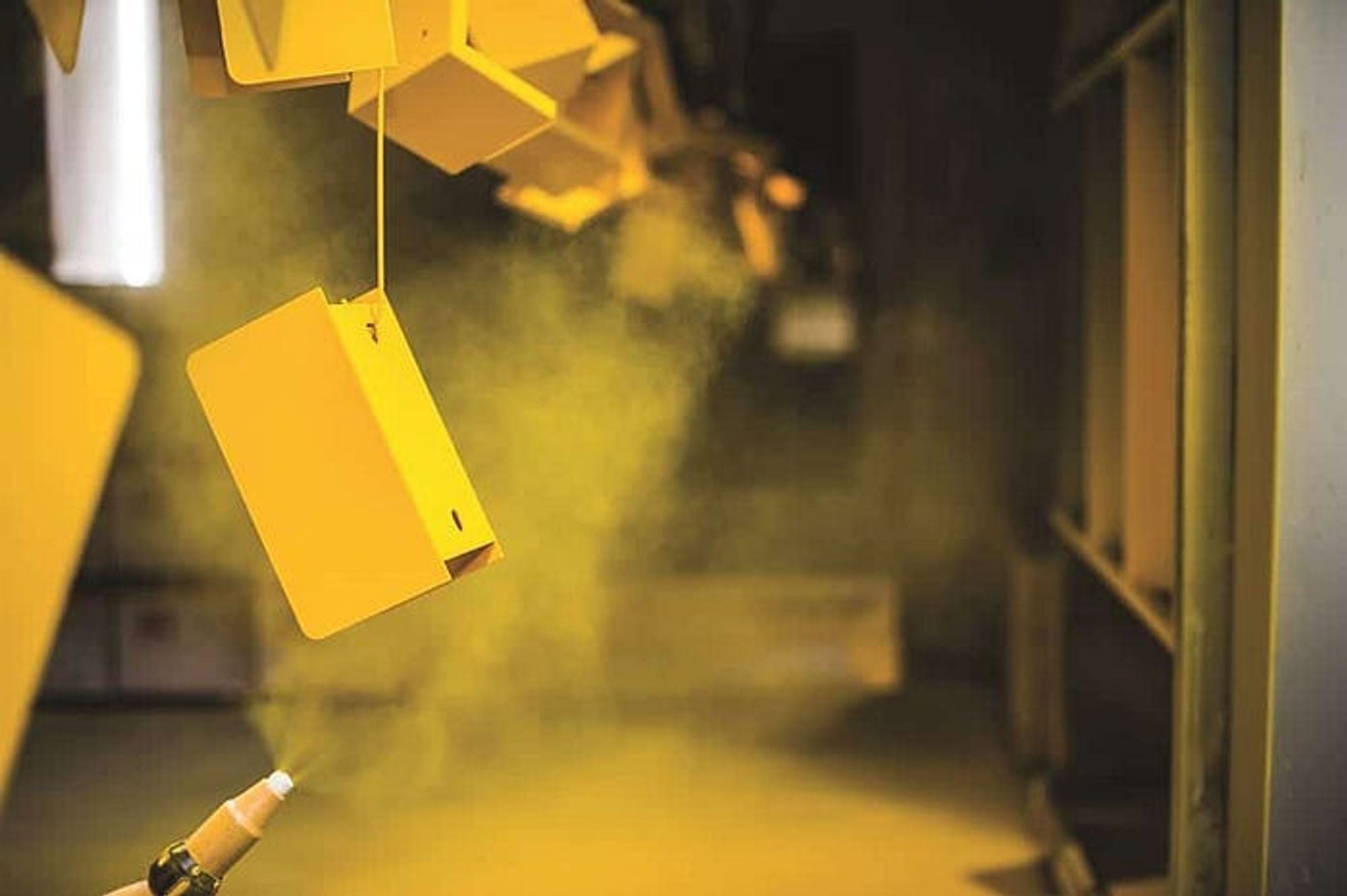
Sandblasting
This mechanical process uses loose abrasive materials such as sand and coconut shells which are propelled at high speeds towards the part driven by compressed air. It is commonly employed to remove contaminants from surfaces, or smoothen a rough surface. Due to the nature of the abrasive media, its effect is similar to that of sandpaper, albeit covering larger surface areas and requiring much less human effort. It is also able to target multiple surfaces at once, unlike conventional sanding machines that can only work on external surfaces, one at a time. Hence, the cost-effectiveness, speed and efficiency of this process makes it a popular method for cleaning parts.
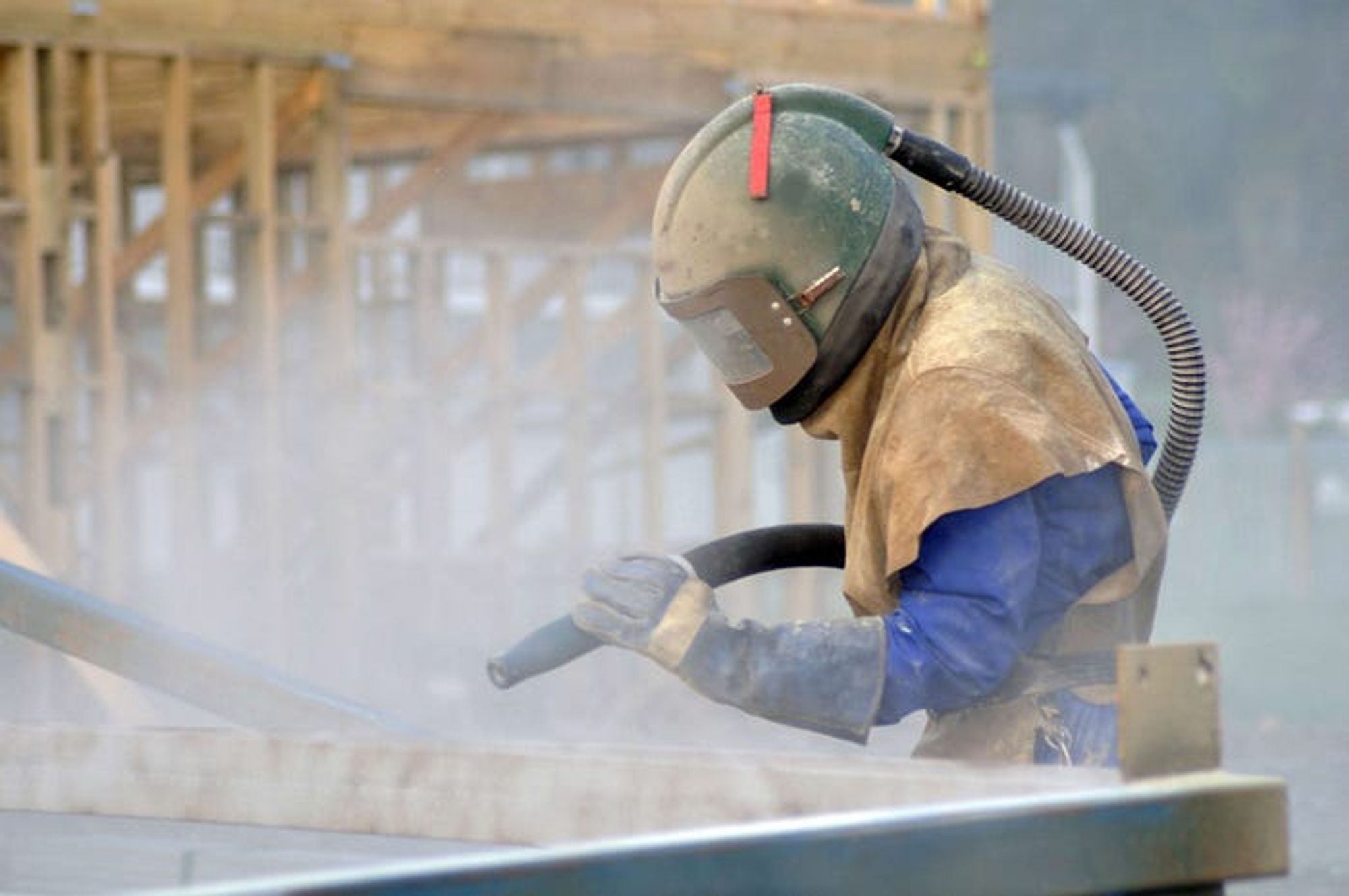
Conclusion
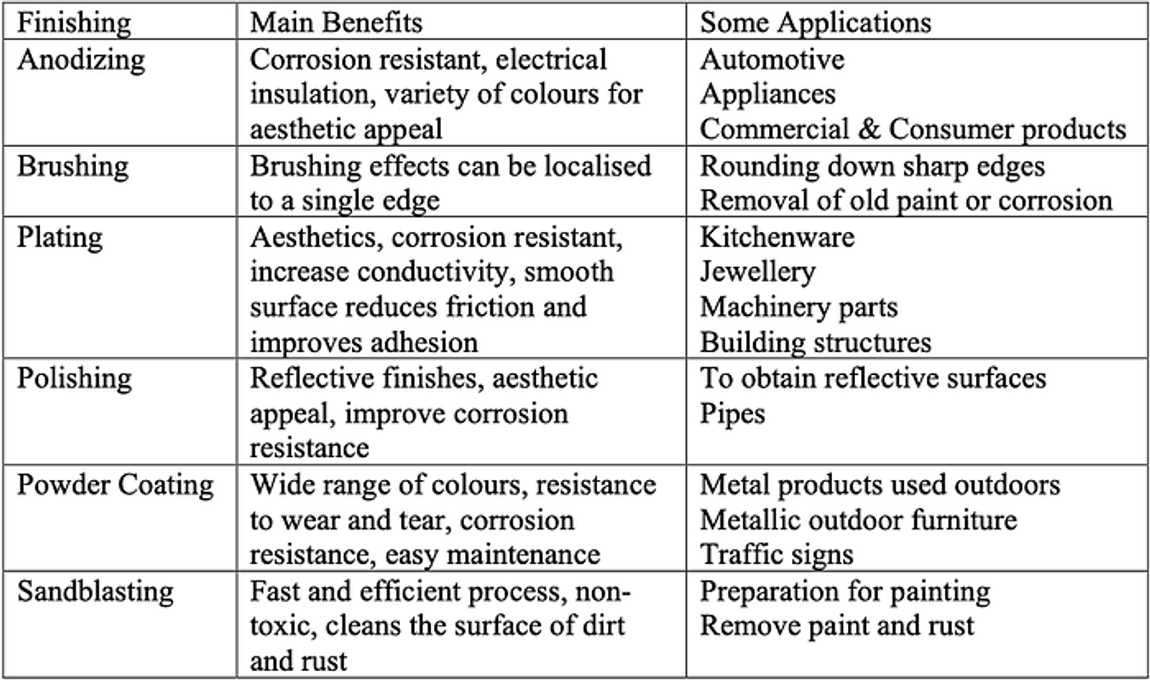
There is a plethora of finishing methods out in the market, with innovative and novel processes introduced every now and then. Depending on the material, purpose and budget, there is a finishing process for every scenario.
At Factorem, we partner with the best surface finishing houses in Singapore to provide the highest quality surface finishing. Get in touch with us as we guide you in achieving the best coatings and surface finish for your needs!
Thank you for reading!