3D printing caters to both hobbyists and professionals alike with its wide range of technologies, from FDM (Fused Deposition Modelling) for quick and easy prototyping to SLM (Selective Laser Melting) expanding the possibilities of metal part fabrication. As 3D printing continues to drive innovation in manufacturing, it is essential to understand how to tackle designs with large dimensions.
While certain industrial-grade printers can handle large parts in one go, many desktop printers have limitations in their printing volume. In this blog post, we'll explore the benefits of splitting 3D printing designs, share tips on how to design parts to be split, and discuss important considerations to keep in mind throughout the process.
How Large Can My Designs Be?
3D printers come in various sizes to suit different needs. Desktop printers have print dimensions typically ranging from 150 - 250mm, and are favored by hobbyists for their short lead times. On the other hand, industrial printers can handle prints with dimensions upwards of 400mm, offering higher precision and the ability to accommodate larger projects.
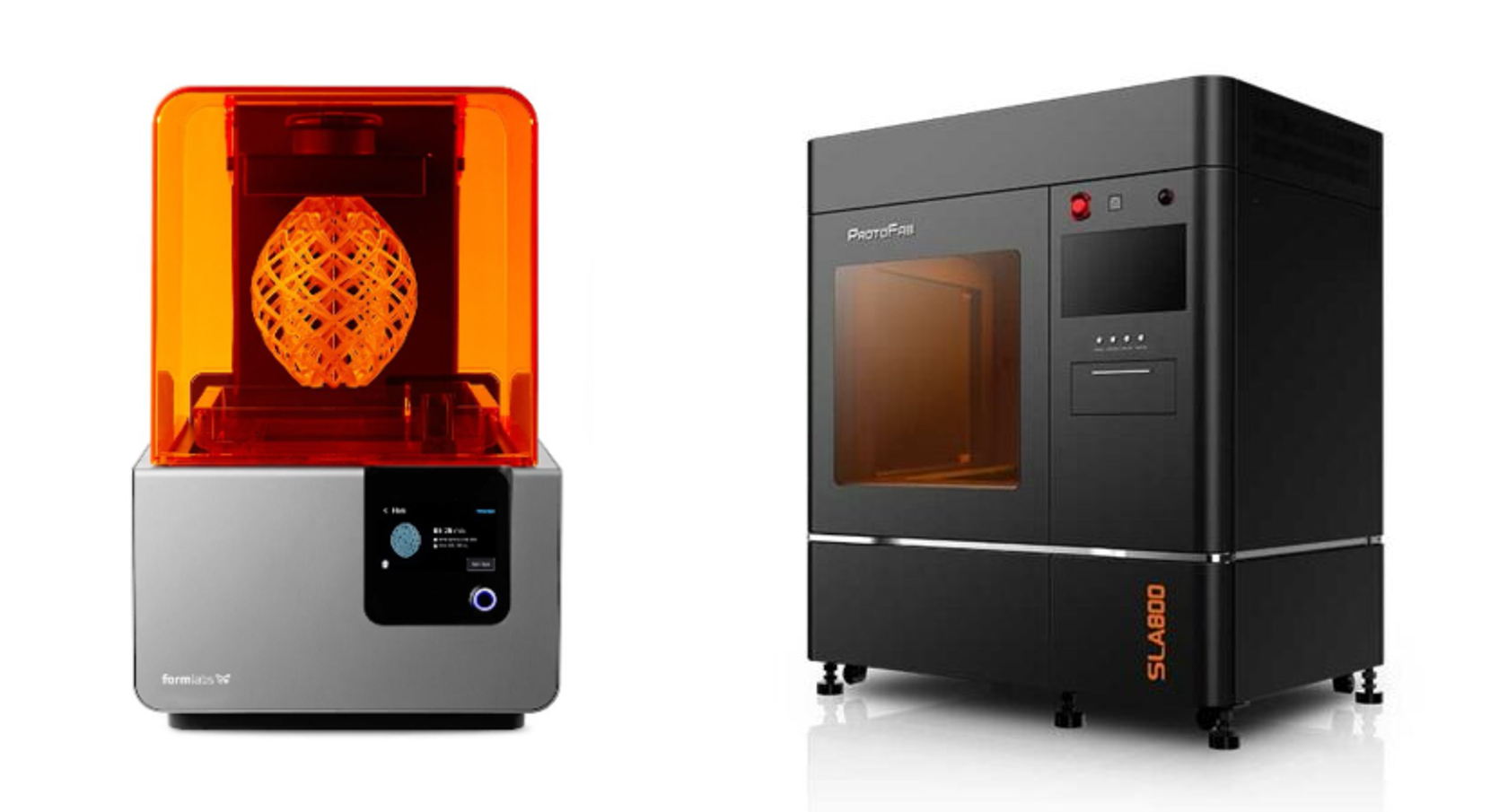
FDM, SLA (Stereolithography), and SLS (Selective Laser Sintering) are utilized in both desktop and industrial printers given their wide use cases. For these technologies, a good rule of thumb is to keep your parts below 220 x 220 x 220mm to ensure compatibility with both types of printers. More complex 3D printing technologies like SLM and MJF (Multi-Jet Fusion) are primarily found in industrial-grade printers. Keeping your parts below 350 x 350 x 300mm allows for greater flexibility in the printing process as they can be accommodated by a wide range of printer models.
If your desired part exceeds these dimensions significantly, it is advisable to split it into smaller segments for individual printing.
Why Should I Split My Designs?
Splitting 3D printing designs offers several advantages that enhance efficiency and cost-effectiveness. By dividing the work among multiple printers, the overall production time can be reduced so that you can receive your prints faster. In the event of failure or wear and tear in using these parts, only the affected segment needs to be replaced, saving costs in the long run compared to reprinting the entire part.
Additionally, splitting designs allows for printing each segment in different orientations. This approach reduces the need for support structures and enhances the mechanical properties of each segment, which minimizes material wastage and increases the lifespan of your part.
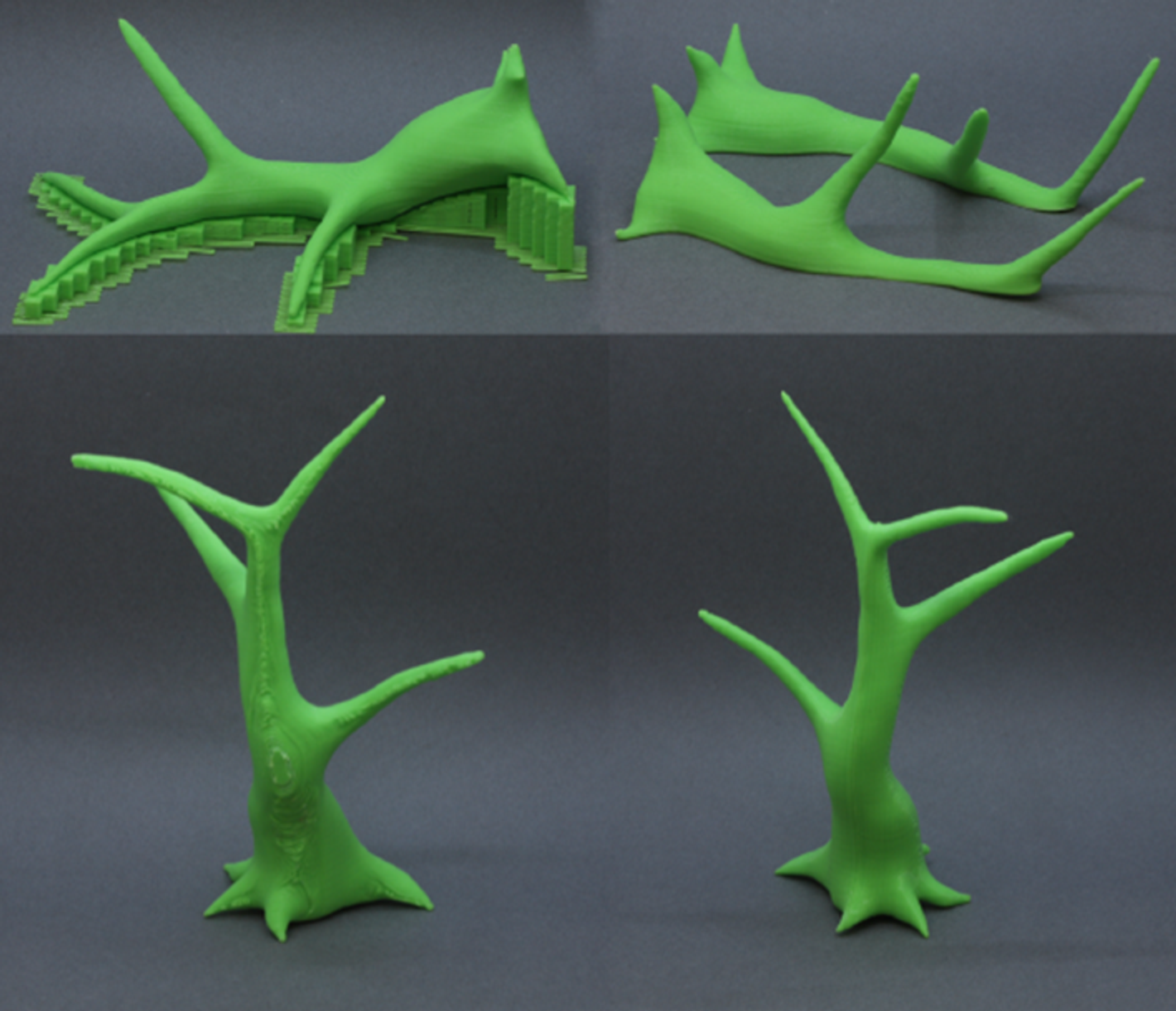
Support structures that are required when printing as a whole (Left) can be eliminated by splitting the part and printing each segment individually (Right). (Karasik et. al, 2019)