Here is an article written by our engineering team that will provide you background information about laser cutting that will help you design sheet metal parts. Sheet metal can be shaped into a myriad of shapes due to its flexibility as explained in our previous articles. However, certain design considerations must be kept in view when designing for sheet metal fabrication.
Do check out our previous articles on sheet metals listed below for a better understanding of how the sheet metal fabrication works.
Tolerance Guidelines for Sheet Metal Design
The following tips are not meant to be strict guidelines and values may differ from manufacturer to manufacturer depending on skills and machinery available.
What is Laser Cutting?
Laser Cutting is a non-contact, thermal process in which a programmed laser cuts the workpiece with a high degree of accuracy. Computer numerically controlled (CNC) laser is guided along the path determined by the design file to trace out and make the required cuts. During the cutting process, a high-energy and intensely focused laser beam is directed at a workpiece which generates metal vapor and melt. These are ejected by a high-pressure gas stream. The laser beam creates a cutting joint or cutting gap in the workpiece, the cutting edge of which can vary depending on the laser beam.
The two most common industrial sheet metal lasers are the CO2 laser and the Fibre laser.
CO2 Laser
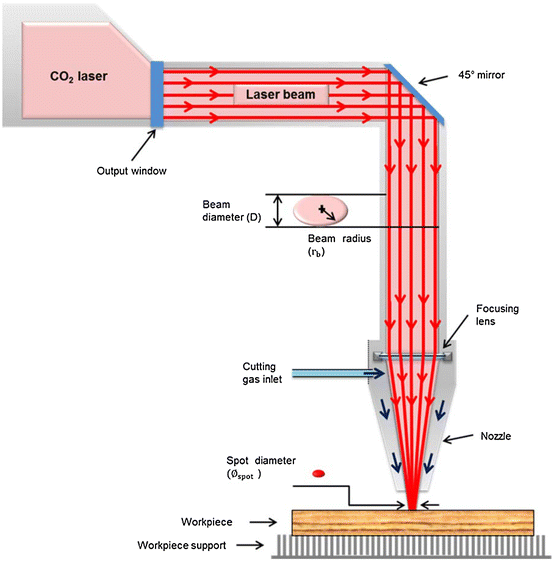
The carbon dioxide (CO2) laser is mainly comprised of 3 gasses: Carbon dioxide, Helium and Nitrogen in the proportion of 4:5:1 respectively. CO2 lasers emit waves at a wavelength of 10.6μm. CO2 lasers are preferred over fibre lasers of the same rating for materials thicker than 5mm owing to their faster cutting times and smoother finish.
Most CO2 laser cutting machines are 3-axis (X-, Y-, Z-) machines. The displacement is produced either by moving the laser head, the workpiece, or a combination of both. The most commonly used method is to keep the workpiece stationary so to as to easily predict and control the movements of an unchanged entity. This method is known as the ‘flying optics’ system. The reverse system, the ‘fixed optic’ system in which the workpiece moves, and the laser is stationary, is better optically but has significant disadvantages when using larger and heavier sheets. CO2 laser usually has a wavelength of 10600nm.
Fibre Laser
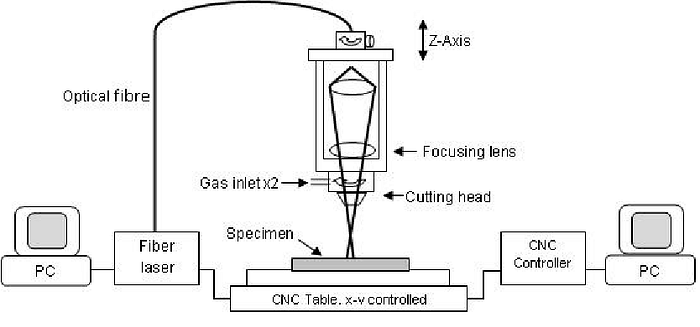
Fibre laser light is produced by a series of diodes and is passed through a fibre optic cable to be amplified. The resulting amplified light is then guided by the use of a lens onto the workpiece to make the required cuts. Fibre laser usually has a wavelength of 1060nm.
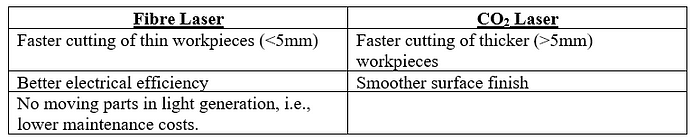
Materials for Laser Cutting
Laser cutting is available for a wide range of materials from paper, wood and acrylic to stainless steel, aluminium and other metals. The maximum thickness of metal plate that can be laser cut varies depending on the equipment each manufacturer possesses but a general guideline to the limit is 25–30mm. Below is a list of materials that can be laser cut and some considerations.
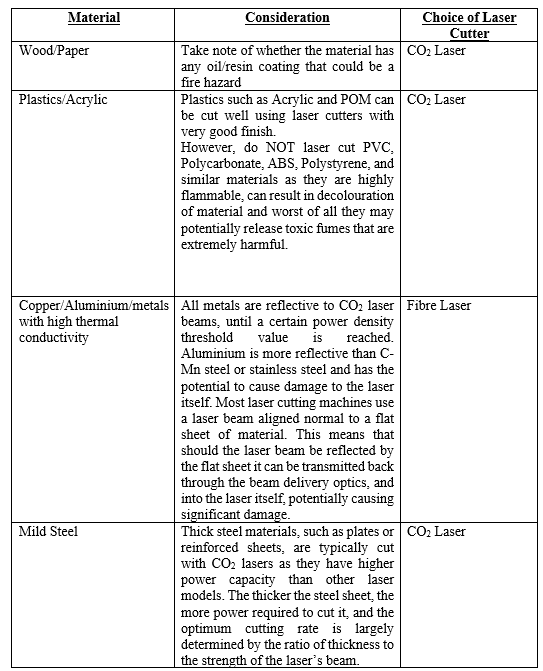
Why Laser Cutting?
While laser cutting requires advanced skill to set up, and often has high initial upfront costs, these pale in comparison to the many benefits that this method of machining offers.
Laser cutting offers the ability to cut different shapes from the same metal plate with intricate details being reflected accurately. There is a +/- 0.1mm accuracy on parts which can be repeated at an accuracy of +/- 0.05mm. This enables mass production of standard workpieces which are excellent replicas of each other without requiring any additional after-treatment.
Compared to traditional thermal cutting methods, laser cutting offers much faster cutting speeds as well as greater automation as modern machines require very little manual labour to operate. Additionally, laser cuts leave no significant burr on the finished product and have a small heat affected zone (HAZ). These properties allow finished products to maintain the strength and dimensions that are requested for by customers without much after-treatment intervention.
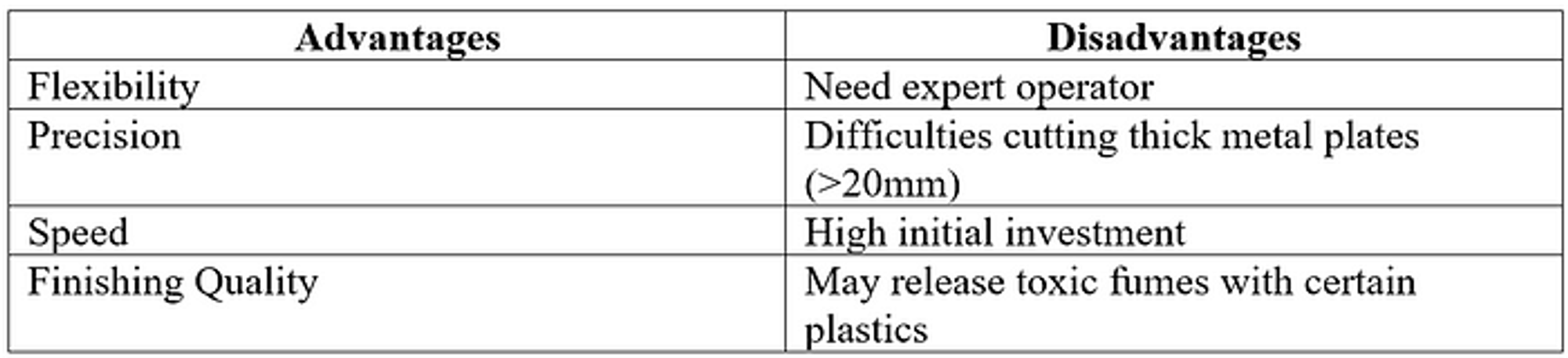
Thank you for reading!