Here is an article written by our engineering team that will guide you through some design considerations for part fabrication using carbon fibre composites. The exceptional mechanical properties of carbon fibre composites make it the material of choice for lightweight and high-performance applications such as aircrafts and race cars. Given its excellent mechanical properties, use-cases of carbon fibre and related composites are endless!
What is Carbon Fibre?
Carbon fibre is a polymer and is sometimes known as graphite fibre. It is a very strong yet lightweight material, five-times stronger than steel and twice as stiff. Though carbon fibre is stronger and stiffer than steel, it is lighter than the latter, making it the ideal manufacturing material for many parts that require weight reduction or a high strength to weight ratio.
Carbon fibre is made of thin, strong crystalline filaments of carbon that is used to strengthen material. It can be thinner than a strand of human hair and gets its strength when twisted together like yarn. It can then be woven together to form a cloth and laid over a mould to be coated in resin or plastic before it finally takes the desired shape.
Carbon fibre reinforced polymers are composite materials which rely on the carbon fibre to provide the strength and stiffness while the polymer provides a cohesive matrix to protect and hold the fibres together and provides some toughness. They can be engineered to achieve mass reductions not achievable by the metals. Since these are artificially composited materials their properties and performance can be tailored to the application through varying strength, length, directionality and amount of the reinforcing fibres and in the selection of the polymer matrix.
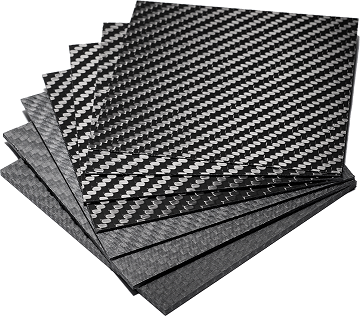
Design Considerations
Material Thickness
As the thickness of the carbon fibre increases, its flexibility decreases as it becomes more rigid. Therefore, a thicker carbon fibre component would be less vulnerable to fatigue and impact damage.
While carbon fibre sheets of thickness less than 0.05” are more suitable for very light structural applications such as surface finishing, a sheet of thickness 0.07” will be able to support light components such as gauges and controls with no backing required. Carbon fibre sheets of thickness 0.09” are ideal for robotic and drone applications while thicker sheets can be used to build production tools and machinery etc.
For applications where weight is a critical element, a sandwich structure may prove to be useful. A composite sandwich sheet combines the superior strength and stiffness properties of carbon fibre with a lower density core material to provide a much higher stiffness to weight ratio than a standard carbon fibre sheet (click here to learn more). The material is commonly used in automotive, truck and mass transit industry due to its superior bending stiffness.
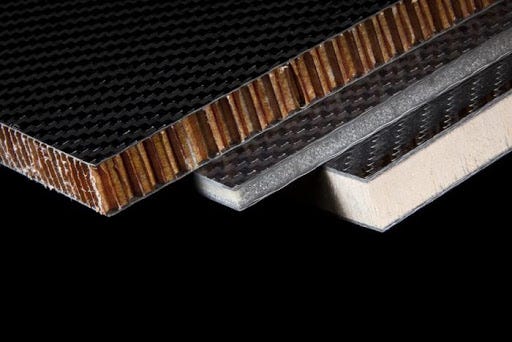
Corner Radius
Corners are points of stress concentration making them vulnerable to failure. A smaller corner radius can significantly reduce the ultimate strength of the carbon fibre structure due to stress concentration around the corner area. The stress concentration factor increases when the corner radius decreases. Radial stress on the carbon fibre sheet decreases with increasing corner radius therefore, the strength can be increased by utilizing a larger corner radius.
Manufacturing
Carbon fibre composite components are manufactured using a moulding process. Moulds are used to define the shape of the composite parts. The graphite composite part will pick up all shapes and features of the moulds; therefore, the quality of the part is heavily influenced by the quality of the mould.
The selection of a proper manufacturing method is dependent on the material used, production volume and complexity of the structure.
A few common manufacturing methods are listed below.
- Vacuum infusion: Commonly used to produce complex structures with polyester and vinyl ester materials. Both small and large parts can be manufactured, with both high/low performance and there are no limitations in part geometry.
- Injection moulding: Used to produce complex parts with thermoplastic resin in high volumes (>1M parts annually).
- Hand and spray lay-up: Used to produce large parts using either thermoset or thermoplastic resins in small volumes. This is the easiest way to manufacture composite parts.
- Liquid moulding: used to produce complex and dimensionally accurate parts with good surface finish. It is also possible to integrate a sandwich core in the parts.
Learn more here
Carbon fibres by themselves have a negative coefficient of thermal expansion (CTE) — meaning that when they are heated, they shrink. The shrinkage for vinyl ester and polyesters are 5–12% but can be significantly reduced by addition of low shrink activities. For epoxy, the shrinking is 1–5%. High resin shrinking eases the removal of the composite from the mould and can be desirable. It can however cause moulding defects, such as warpage and shrink marks therefore, the shrinkage should be controlled by heat treatment to minimize defects.
Fire Resistance
The most common materials used when fire resistance is of utmost importance is Phenolic resins (thermosetting) and Polyphenylene sulphide (thermoplastic) due to their superior fire resistance properties and high thermal stability.
However, flame retardants can be incorporated into any carbon fibre composite as a simple additive compound blended into the polymer matrix or in the form of heat-resistant coatings. The introduction of brominated epoxy vinyl ester resins delivered fire retardancy in addition to corrosion resistance.
Insulating coating is the common way to protect composites from fire, and the ideal coatings should at least meet the requirements of flame retardancy, low thermal conductivity, strong adhesion to the substrate, durability, and wear resistance.
General Design Guidelines
Carbon fibre composites offer unmatched performance for lightweight, high-strength applications — but maximizing their potential starts with smart design and expert manufacturing. Whether you're building aerospace parts, automotive components, or robotics systems, understanding the nuances of material thickness, corner radii, and fabrication techniques is essential.
At Factorem, we simplify the complex. From design support to production, we connect you with experienced manufacturers who specialize in carbon fibre composite parts — so you get the performance you need without compromise.
Ready to bring your carbon fibre design to life?
👉 Get a quote now at https://app.factorem.co/getquotenow and work with trusted partners who know composites inside out.