Here is an article written by our engineering team that will guide you through choosing your material for 3D printing, difficulties behind printing with these materials and why it is so expensive.
1. Polylactic Acid (PLA)
PLA is the most common material used for hobby level printing as well as being one of the cheapest materials available for prototyping. It is commonly used in Fusion Deposit Modelling (FDM). PLA comes in an array of colors as well. However due to its low glass transition temperature (Tg) of 50–60 degrees it is prone to deformation if used in high temperature or outdoor environments.
PLA has surprising amounts of fracture resistance with an ultimate tensile strength of 65MPa should your design allow for deformation.
High temperature PLA (HTPLA) is a type of PLA that allows the material to be heat treated in the oven. The heat treatment changes its material structure from amorphous to crystalline. This allows it to have a much higher melting temperature (Tm) over 150degrees before it starts to deform unlike normal PLA which does not have a defined temperature which it deforms at.
PLACTIVE is another type of PLA in which copper is infused into the filament. The copper nanoparticles are said to be highly effective in eliminating fungi, viruses and bacteria which makes it great for medical use.
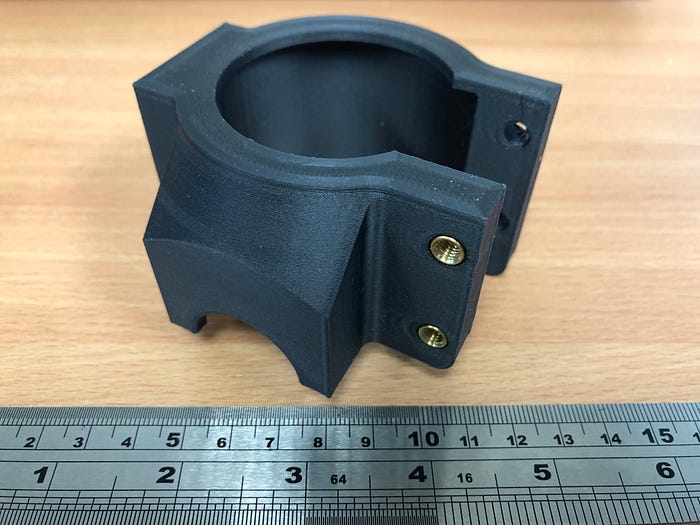
2. Polyethylene Terephthalate Glycol modified (PETG)
PETG has a soft surface which makes it vulnerable to wear but is more flexible compared to PLA. Its durability is much higher than PLA, partially due to its higher glass transition temperature which makes it a better option for mechanical components compared to PLA. Due to its better mechanical properties, PETG can be both plastic welded and machined.
However, PETG is more expensive compared to PLA and not commonly used in industrial application despite the pros described.
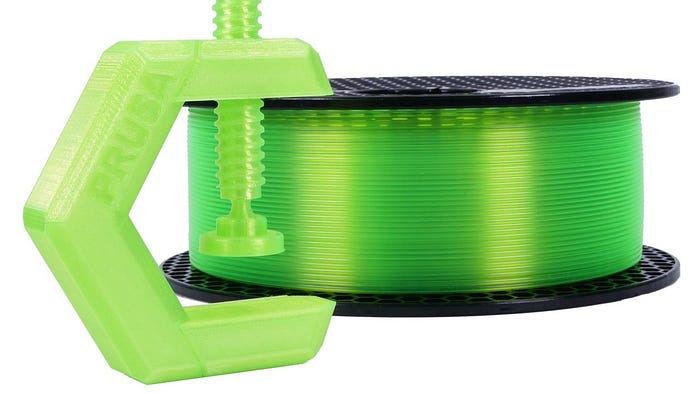
3. High Impact Polystyrene (HIPs)
HIPS has high impact strength, 30% lighter than PLA and cheap in terms of material cost. However, it requires a heated enclosure and a specialized surface for it to be printed on making it costly to print. Additionally, due to the need for a heated enclosure, parts that are not designed for support less additive manufacturing (especially FDM) will be difficult to print and likely require splitting and gluing of the part to ensure the design is able to be printed in the first place.
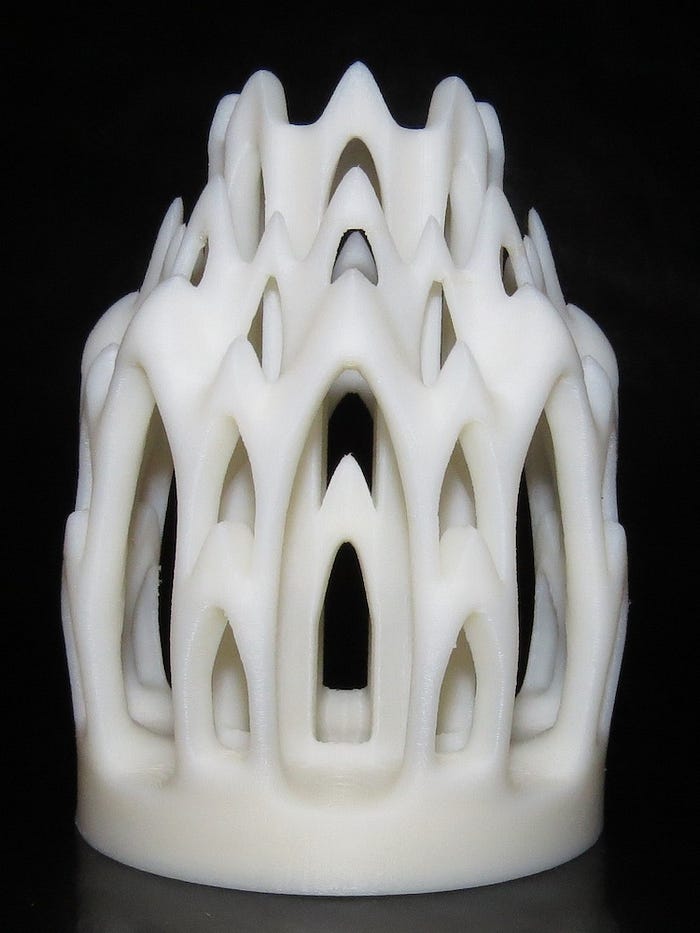
4. Polypropylene (PP)
PP has high impact, fatigue, and heat resistance. It is also extremely flexible, waterproof and is watertight which is why it is used for household bottles such as shampoo bottles.
However, the semi-crystalline structure means that it needs to be printed in a heated enclosure which makes it prone to warping and difficult to print parts that are not specialized for additive manufacturing. Likewise, polypropylene’s inability to stick to common surfaces means special glue sticks need to be used which increases costs. Furthermore, the material itself is expensive which means printing a PP part is expensive overall.
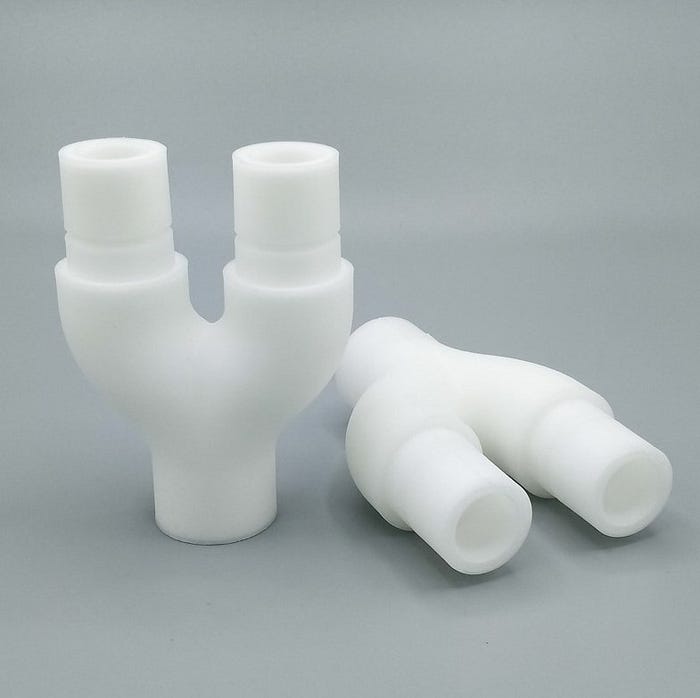
5. Acrylonitrile Butadiene Styrene (ABS)
ABS, the go to plastic for cheap prototyping as it is known for its high temperature resistance and decent mechanical properties.
While commonly used in molds, it can only be printed using FDM and SLA technology.
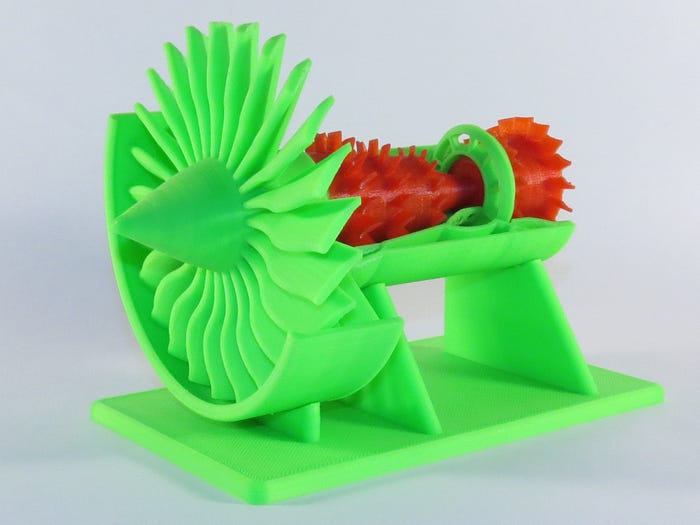
ABS is cheap in terms of material costs. In terms of mechanical properties, it has good impact, wear and heat resistance which makes it a good choice for most applications. It is also commonly used for 3D printing injection molds.
However, it requires a heated bed and enclosure to ensure the print does not warp which again makes any prints with supports or designs that are not catered to additive manufacturing difficult. Furthermore, ABS tends to shrink after cooling which means it will not be accurate and needs to be considered in the design phase or be considered by the manufacturer when printing.
If you require your print to be smooth on the exteriors do ask for a vapor smooth acetone finish!
6. Acrylic Styrene Acrylonitrile (ASA)
ASA can be seen as the superior ABS with its improved UV resistance, high impact strength and higher temperature resistance compared to ABS. Similar to ABS, it can have a smooth finish by using acetone.
However, due to its improved mechanical and chemical properties, the cost of printing ASA is significantly larger compared to ABS. Likewise the difficulty with ABS exists with ASA due to similarities in the mixture.
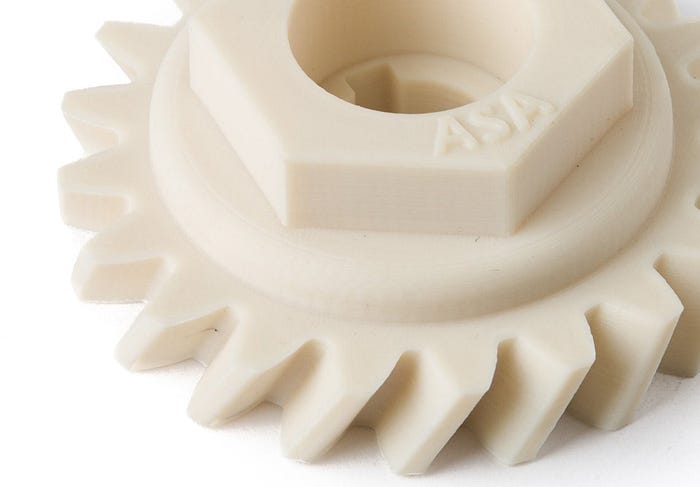
7. Thermoplastic Elastomer [TPE]
TPE is extremely elastic with its low shore hardness of 84A. However due to its low shore hardness, if it is to be printed on using FDM, it is extremely costly and difficult to print due to needing just the right amount of pressure.
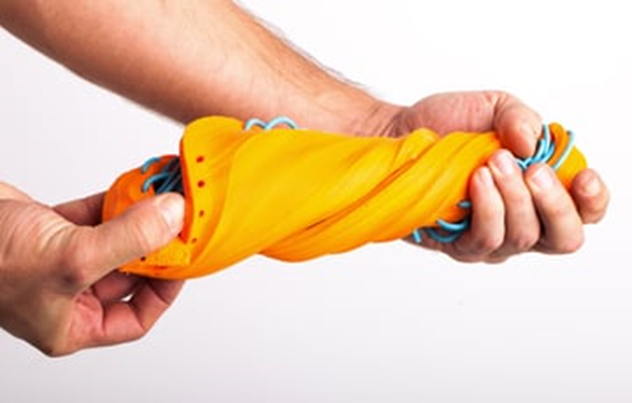
8. Thermoplastic Polyurethane (TPU)
With a shore hardness of 90–98, it is not only flexible but is strong and durable as well. However, due to its flexibility and tendency to absorb moisture it is difficult to print which means an overall increase in cost. Likewise, due to the flexibility, if printed on FDM print speeds needs to be slow to ensure consistent extrusion of the filament which increases lead times and cost compared to another non-elastic filament.
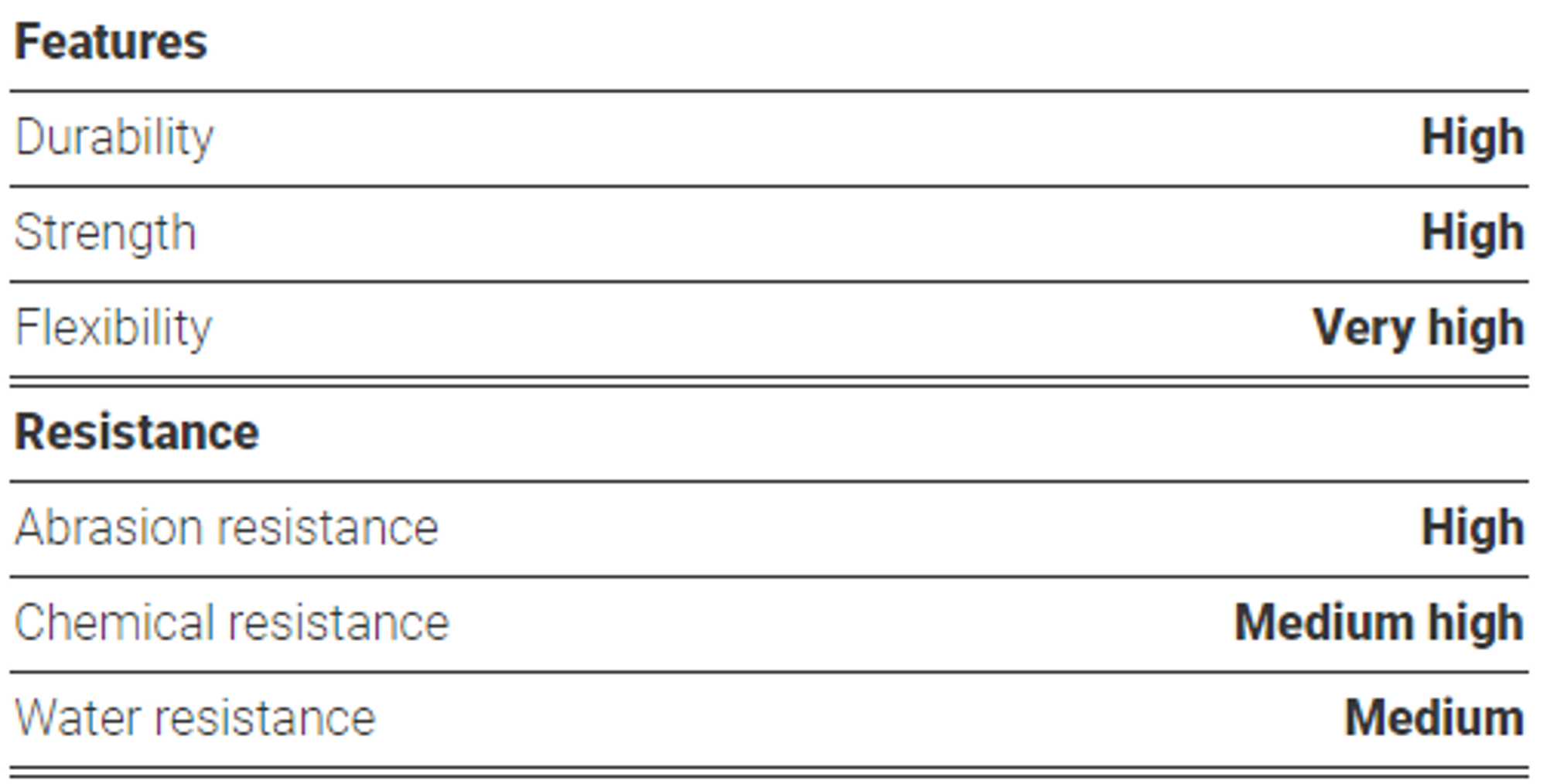
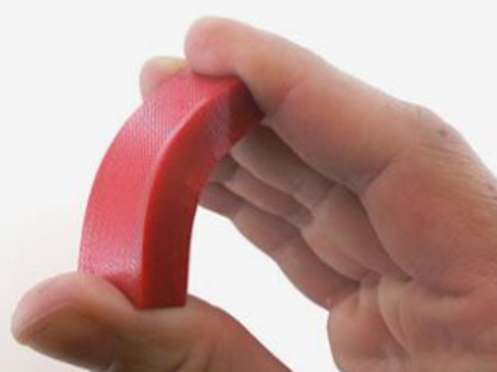
9. Polycarbonate (PC) — Engineering plastic
Polycarbonate is one of the few commonly used plastic that is transparent along with acrylic. However, unlike acrylic polycarbonate possess high mechanical properties which makes it ideal for functional or load bearing parts.
Polycarbonate is commonly used to create prototypes for windows or other clear products that would cost much more to have the same mechanical properties. However careful designing of parts is required to ensure that the part can be manufactured.
PC has high tensile strength, heat deflection and high impact resistance. Additionally, its high glass transition temperature of 150° C. However, unlike PC sheets which are extremely rigid and tough, printed PC is more flexible.
Likewise, due needing a heated enclosure of about 110° C and 275° C for PC to be melted, higher end equipment is needed which means costs would increase significantly as well. Likewise due to polycarbonate being hydroscopic (easily absorb moisture from air), special storage equipment such as dry cabins are needed to ensure moisture is not absorbed by PC.
Like PLA, PC can be infused with Carbon Fiber to make the structure more rigid.
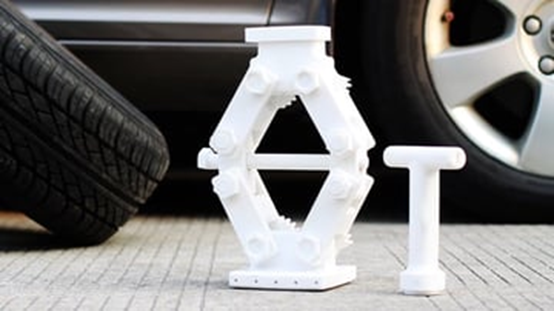
10. Nylon — Engineering plastic
Nylon/ Polyamide is well known for its toughness and flexibility as seen in its use case in fishing. Moreover, nylon has high impact and good abrasion resistance. However, unlike the other engineering plastics discussed, Nylon is relatively easy to print. This would likely mean that its cheaper in terms of hardware costs. However, the cost of Nylon as a material is much higher compared to the cost savings from being easy to print which makes Nylon expensive as well.
Nonetheless, Nylon is extremely hydroscopic which means that special storage solutions such as a dry cabinet is required especially in Singapore’s climate which is known to be humid and moist for filament-based nylon. This increases the cost of printing nylon as well.
Despite all of this, if what you are looking for is a material that is the most value for money, Nylon is your go to interns of cost to performance ratio. To eliminate the issue of Nylon being flexible, try out Nylon 12 Carbon Fiber (Nylon 12 CF), by adding carbon fiber into the mix it rigidifies nylon without adding too much weight to it.
Commonly used nylon types available at Factorem are Nylon 12, Nylon 12 Carbon Fiber, Nylon 11 and Nylon PA2200.
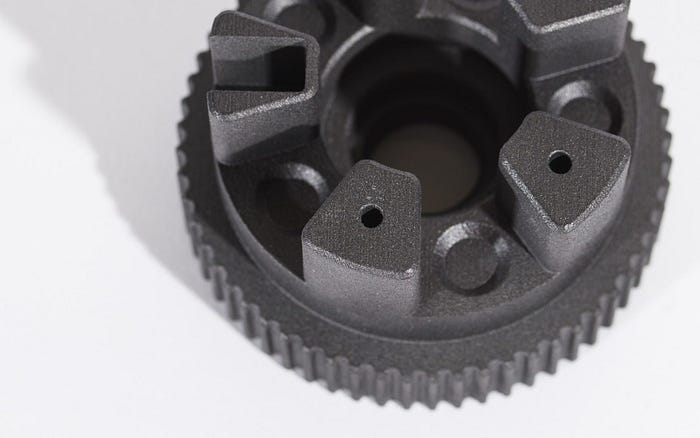
11. Delrin/POM/Acetal — Engineering plastic
Delrin is stiff, stable, durable, tough, chemical resistant, and extremely low coefficient of friction. While it does not require high temperatures to melt, the struggle is to have Delrin stick to any material. As such special print beds or wood beds are required. This will drive up the cost of producing a Delrin part.
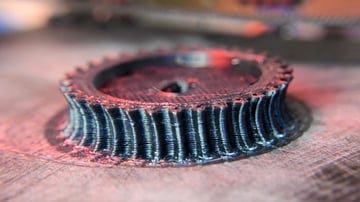
A plus side is a printed Delrin will often be smooth. Its mechanical properties are like no other plastic and thus commonly used for mechanical parts such as gears, bushings and bearings. Additionally, printed Delrin parts can be CNC-ed to achieve a higher level of dimensional accuracy.
Furthermore, due to its high stiffness even when melted, Delrin can only be printed at a slow speed. Likewise due to it producing formaldehyde when melting in addition to needing a vacuumed heated enclosure, the structural cost required to print Delrin is high. Lastly, the material itself is expensive which makes printing Delrin an extremely difficult task and why suppliers quote such a high price when printing Delrin.
12. Polyether Ether Ketone (PEEK) — Engineering plastic
PEEK is one of the most expensive materials available in Additive manufacturing and is one of the strongest plastic available. While it is mostly used for FDM 3D printing, SLS 3D printing of PEEK is available as well. More interestingly, PEEK is completely flame resistant making it usable for gun parts.
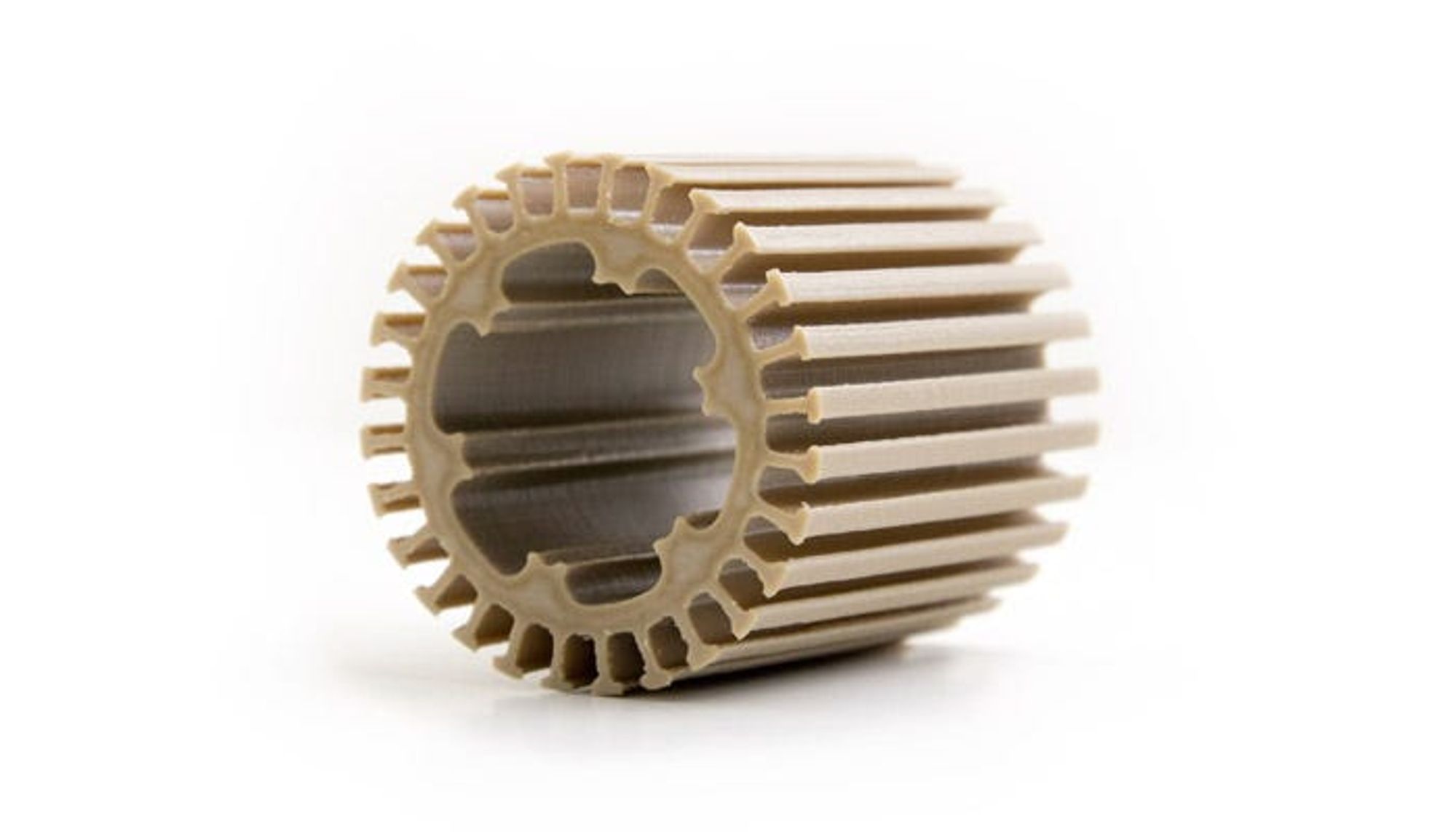
Due to its weight to strength ratio and wear resistance it is used in the aerospace, medical and automotive industries to substitute metals in some parts.
13. Conclusion
When designing a component, the design goals and requirements are critical in identifying the correct material and additive manufacturing technique to choose form. The above is an extracted table showing the important general details of some of the materials that were discussed. However, do note not all of the material have the same material structure and is best to check with us if your part requires specific material characteristics.
Some of the more commonly used 3D printed materials were discussed in this paper, however for liquid and powder-based materials there are other options available which were not stated in this whitepaper. While material choice is important, it is also important to look at the technology used to print these parts as the materials list available for each technology differs. Do keep a lookout for future articles by Factorem and follow us on our journey to #HelpMakersMake.
Thank you for reading!