How much does it actually cost to 3D print and when should you switch to injection molding?
Fused Deposition Modeling (FDM) is the preferred 3D printing method for fabricating products that are still in the early development stage and are likely to experience design changes, as FDM 3D printing can easily adapt to said changes while also being relatively low cost.
However, even when the design has finalized, some companies may still choose 3D printing as it has been shown to be effective with their product and is still able to meet the demand.
For in-house FDM fabrication of products, the retail price to customers might be broken down as follows:
Material Cost
- Filament
- Type: ABS, nylon, TPU, etc.
- Weight used: Dependent on the product’s volume and complexity (PrintAWorld, 2021)
- Sandpaper, paint, etc. (for post-processing, if applicable)
Machine Cost
- Printing on Enders vs Prusas vs Ultimakers
- Machine Depreciation: With every print, the value of the machine drops, and regular maintenance of the machine is required to prolong its useful lifetime
Overhead Cost
- Labor: Machine/Print set up, monitoring/collection of print, post-process (sanding, painting, etc.)
- Office Rental, utilities (electricity, etc.)
- Building your product / R&D
- Profit Margin
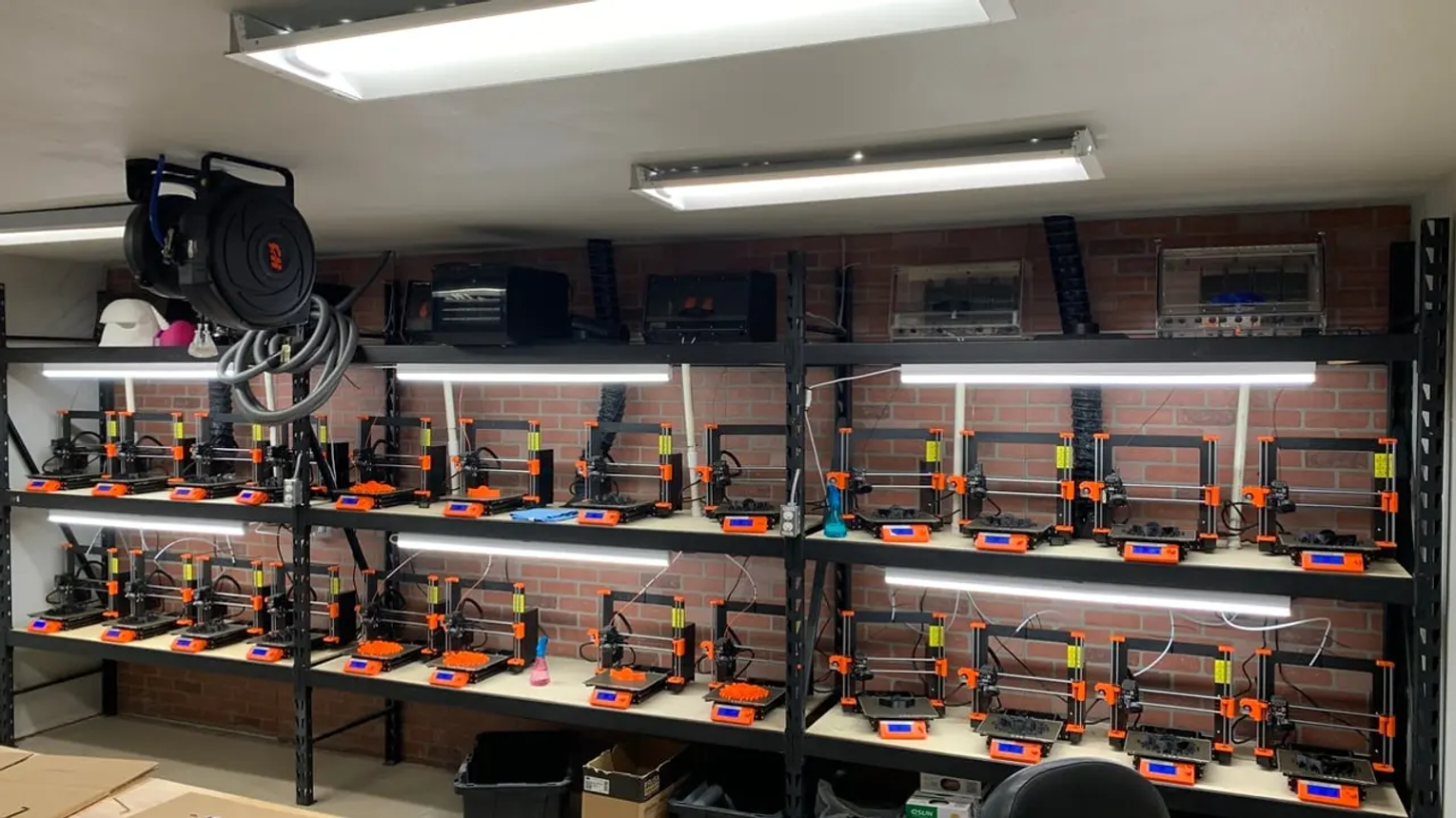
Though the retail price for consumers can be kept reasonable through 3D printing, it is not a sustainable option in the long term as it is time-consuming to print and manage prints. Even if more 3D printers were obtained to meet the demand, there would still be issues with lead time, and this would just mean more assets to maintain. It is important to note that not all 3D prints are perfect. Sometimes, a print may be defective and have to be disposed of after a whole day of printing.
The table below shows the amount of time taken to print a product using the FDM method: