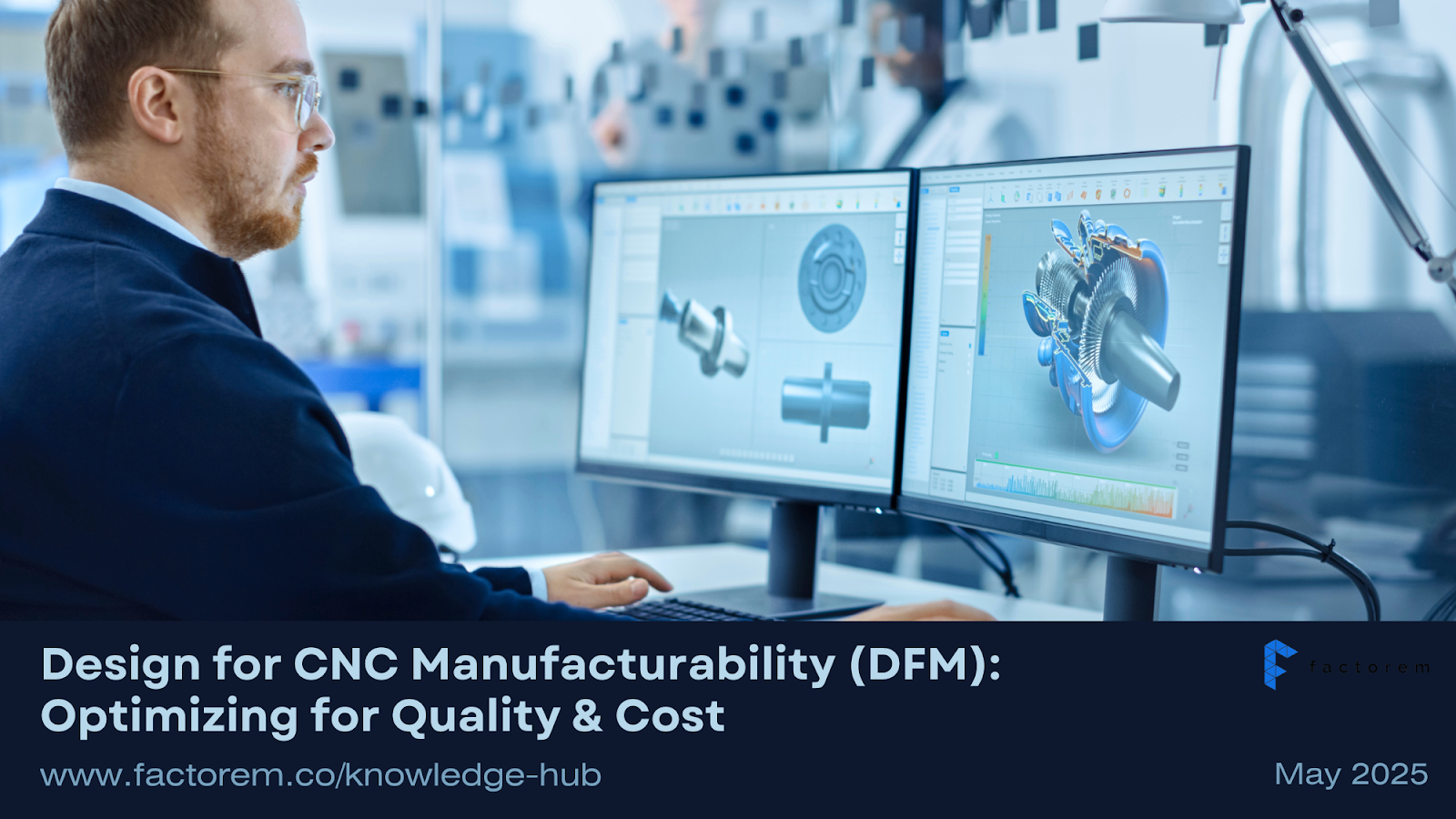
CNC machining has revolutionized manufacturing, enabling precise, intricate designs across various industries. However, in order to harness its full potential; a solid grasp of CNC-specific design principles are critical. Whether you're a seasoned engineer or just getting started with CNC machining, getting a grip on these guidelines is your ticket to creating efficient, cost-friendly, and easily manufacturable designs.
In this article, we will be diving into some things you should look out for to ensure that your design is efficient, cost-effective and ready to be machined! It serves as the foundational chapter in our comprehensive Ultimate Guide to CNC Machining.
1. Deep Pockets
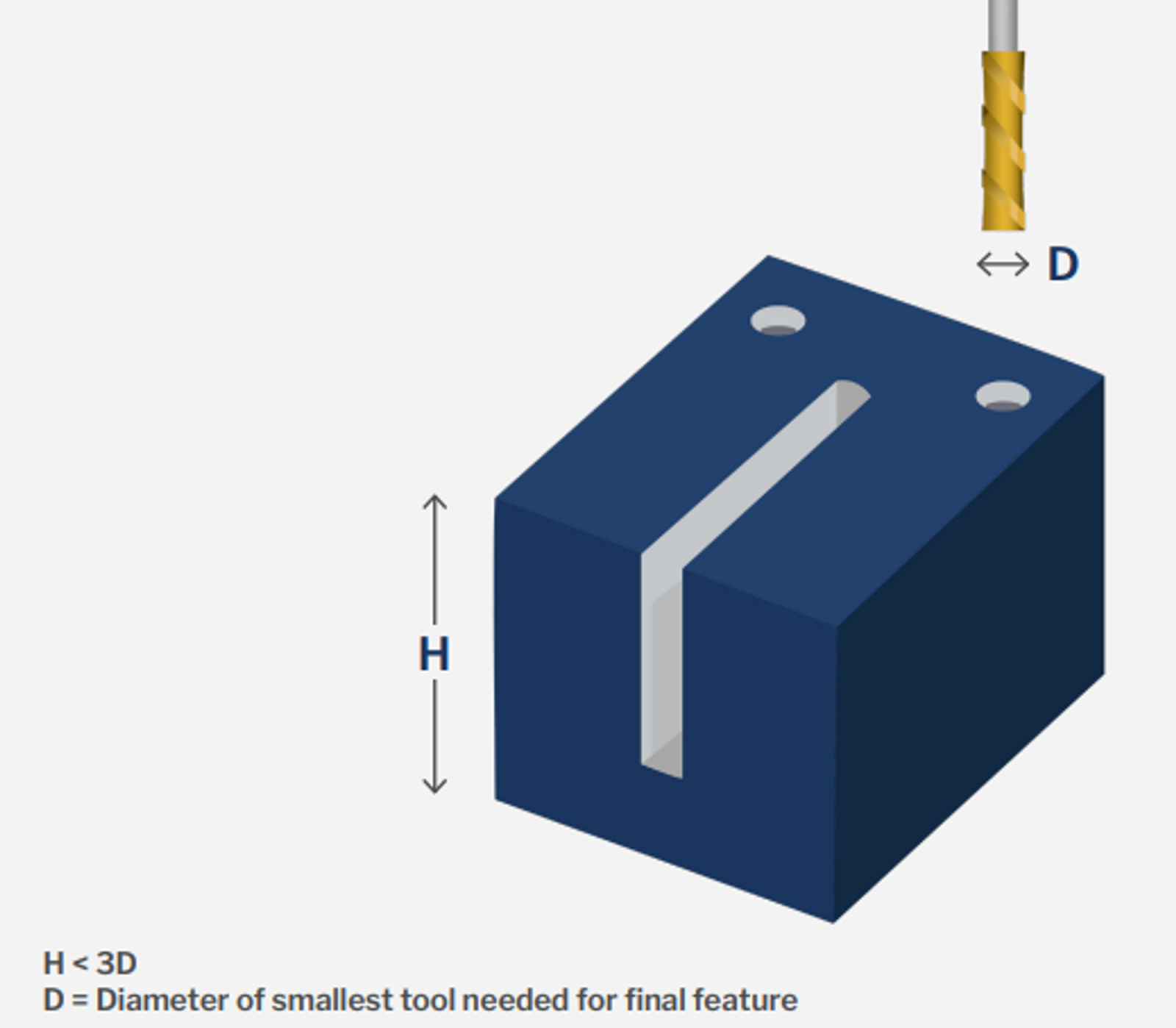
Deep holes and pockets could cause issues that affect the finish and precision of your part or even cause tool breakage. Such features also often require several cuts to be machined properly, which increases machining time, consequently increasing the cost of your part.
Deep Pockets & Holes
- If diameter of hole/smallest cutting tool required is <2mm, maximum recommended depth is 3x diameter of hole/smallest cutting tool required
- If diameter of hole/smallest cutting tool required is >2mm, maximum recommended depth is 5x diameter of hole/smallest cutting tool required
2. Narrow Regions
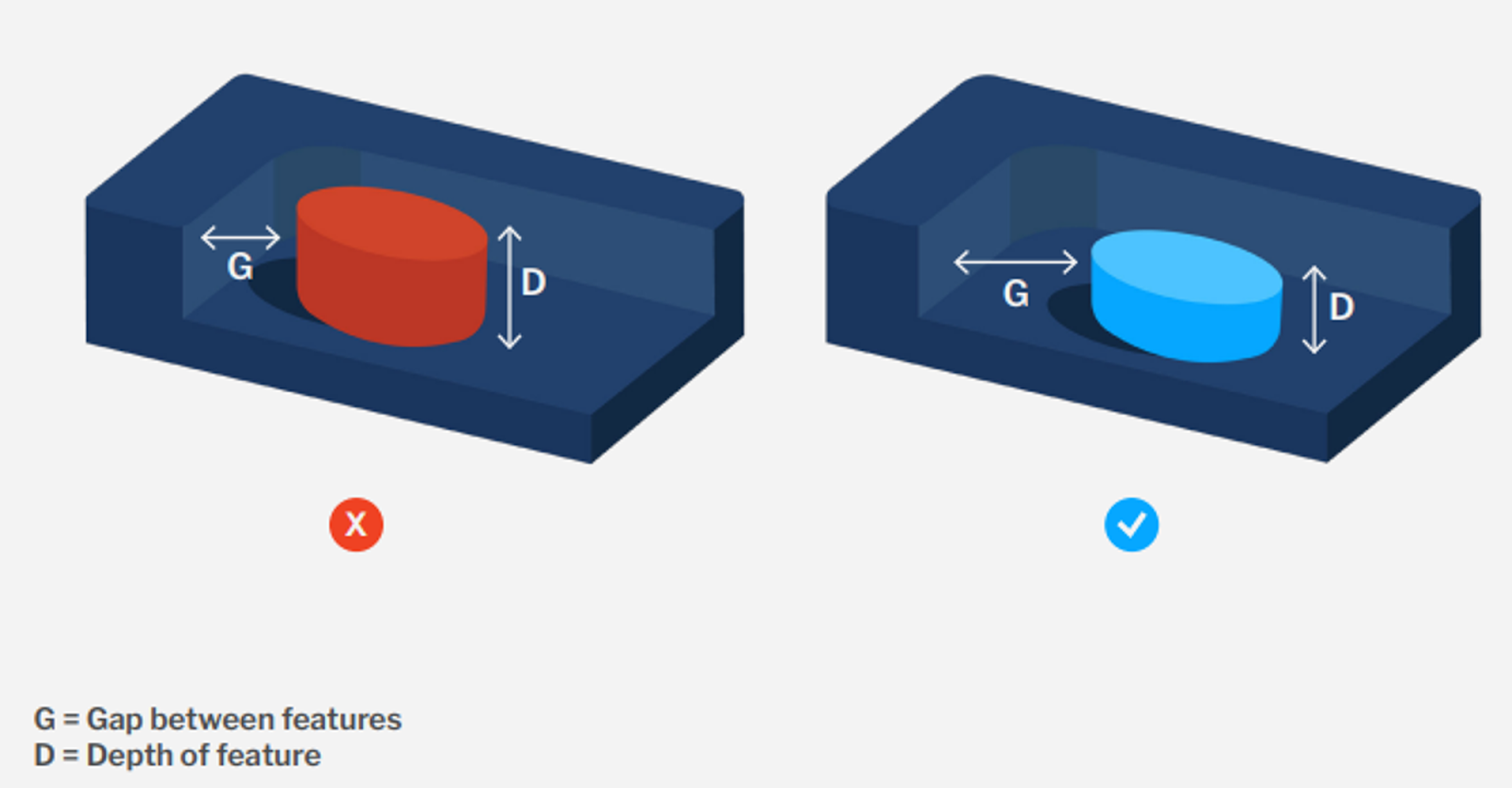
Having narrow regions (tight gaps between features) that are deep limit the tool sizes that can be used, forcing manufacturers to use long, small diameter tools which are more prone to chatter and breakage. This not only increases machining time but also reduces part quality.
Thus keep the gap of narrow regions (gap between features) to no less than 3x the diameter of the smallest cutting tool used and minimize the depth of such features. the
3. Sharp Internal Features
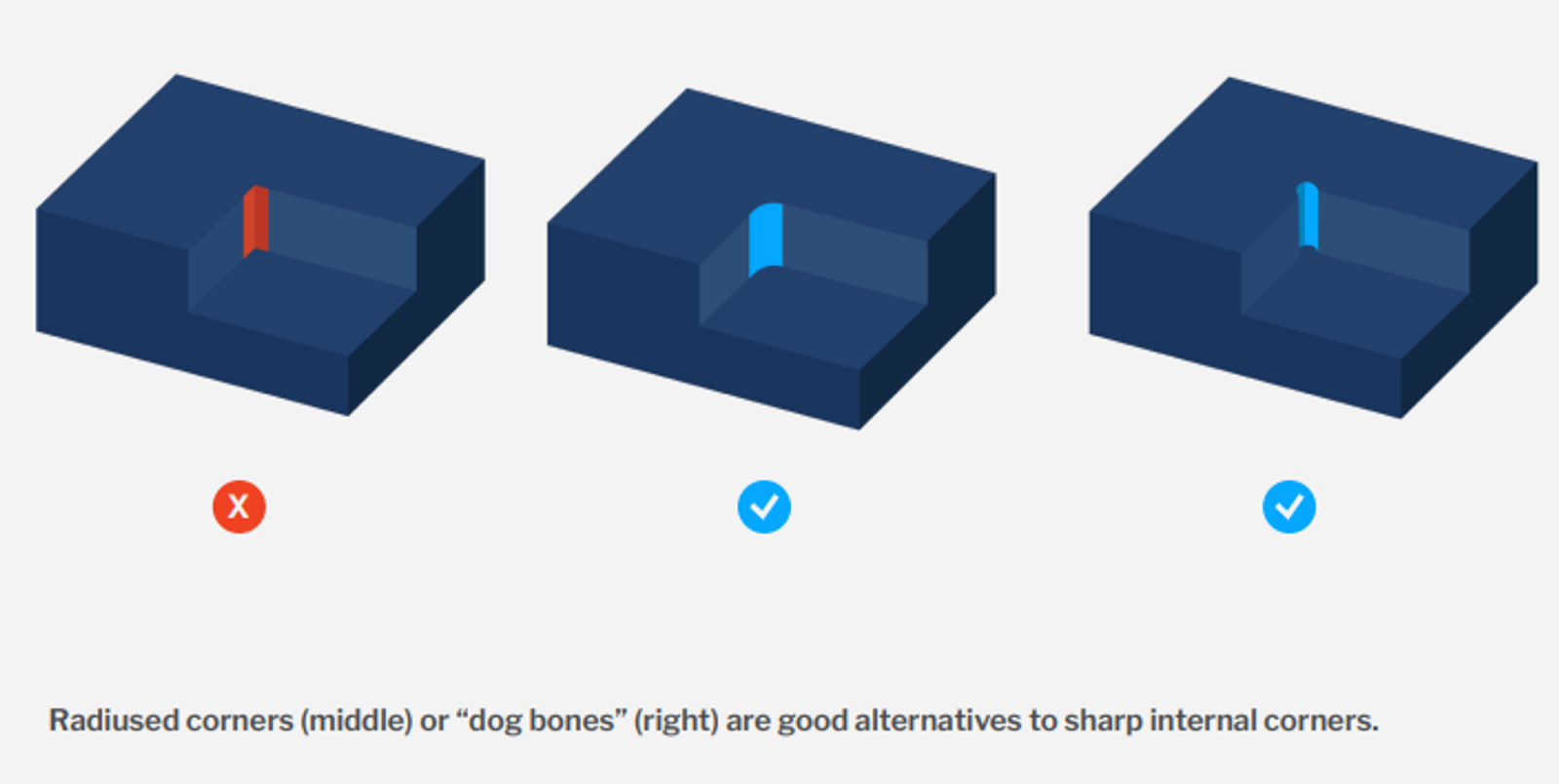
As CNC endmills are circular, it’s resulting cut will leave behind a radius making sharp internal corners difficult to produce without using other more costly methods.
To avoid increasing the tooling cost of your part, opt for internal fillets or “dog bones” instead and stay away from sharp internal corners.
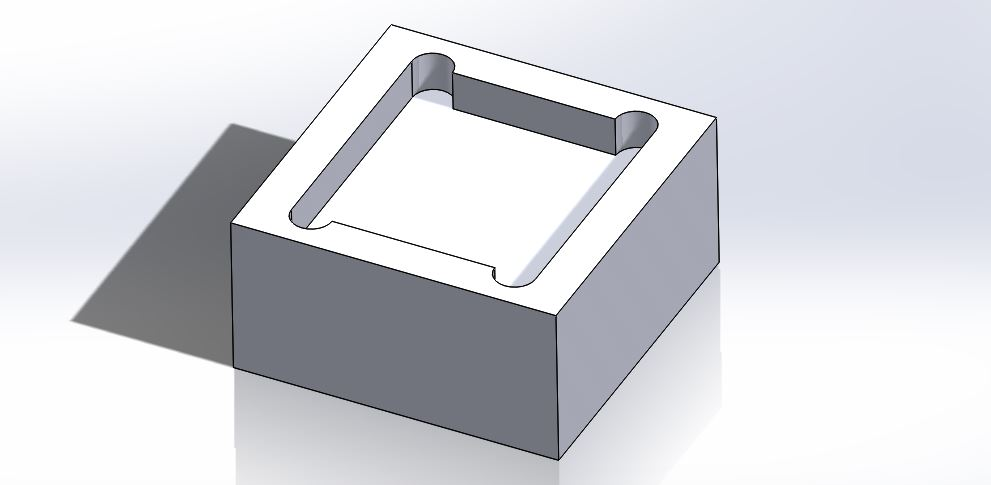
Example of using “dog bones” to avoid sharp internal corners.
4. Thin Walls
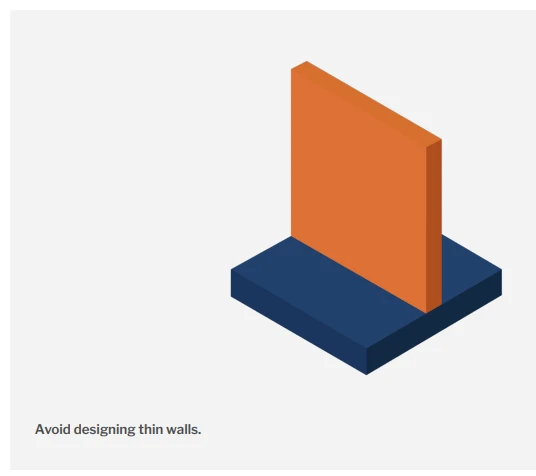
Thin walls can be tricky to machine as they are more prone to vibrations, lowering the achievable accuracy. Maintaining an appropriate wall thickness is crucial to ensure structural integrity, manufacturability, and cost-effectiveness.
Here are the general guidelines to follow:
Metals
- Recommended Minimum Wall Thickness: 0.8mm
- Absolute Minimum Wall Thickness: <0.5mm
- If necessary a wall thickness of 0.5mm is possible, but it may lead to higher machining costs and potential issues with part strength and stability, thus it is not advisable.
Plastics
- Recommended Minimum Wall Thickness: 1.5mm
- As plastic is more susceptible to warping and softening a higher wall thickness is recommended to avoid complications during machining.
5. Chamfers > Fillets
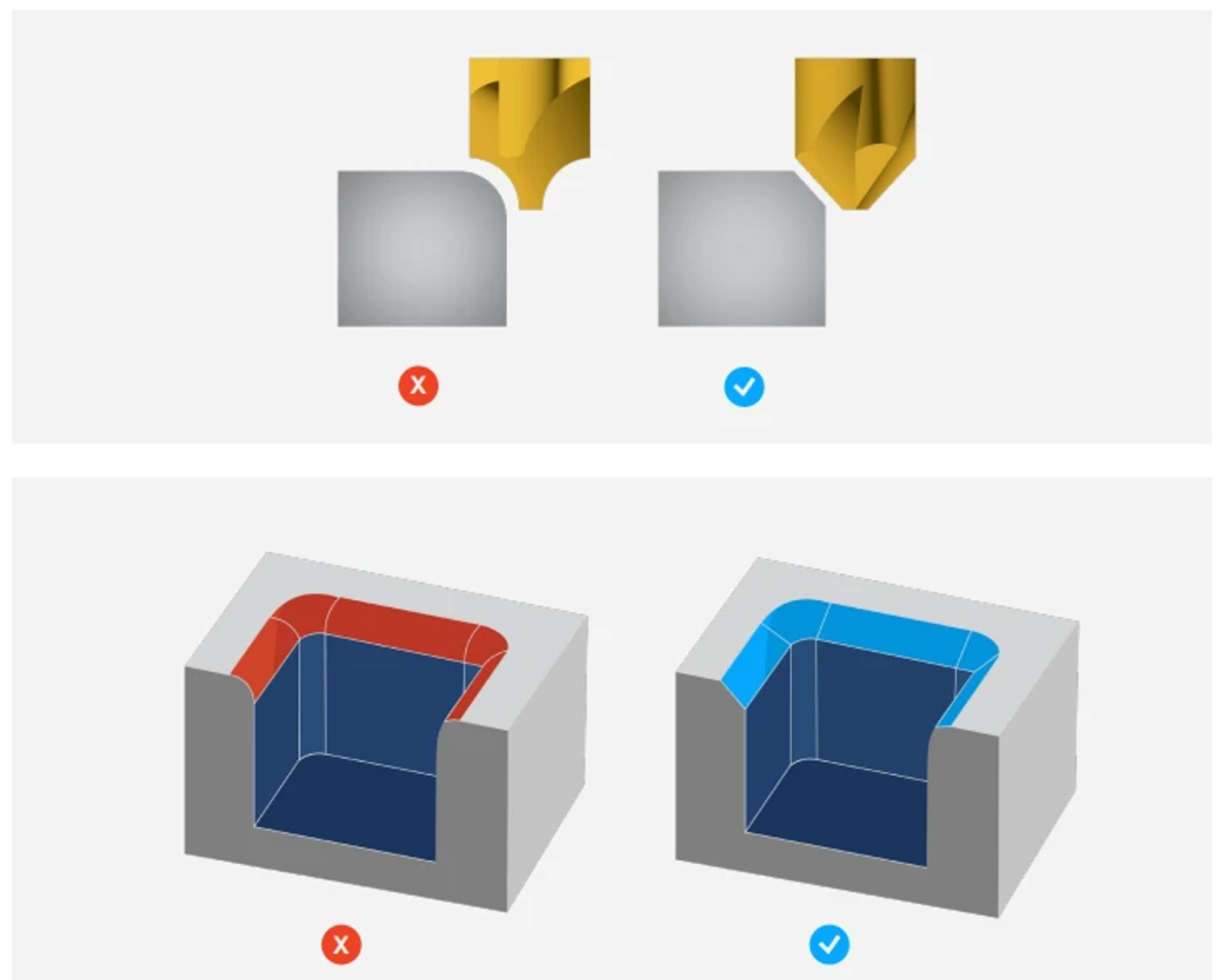
Creating outside fillets generally require more machine time and special tools which can unnecessarily drive up the cost of your part.
Choosing chamfers over fillets whenever possible can help guarantee a cost efficient design.
6. Inaccessible Features
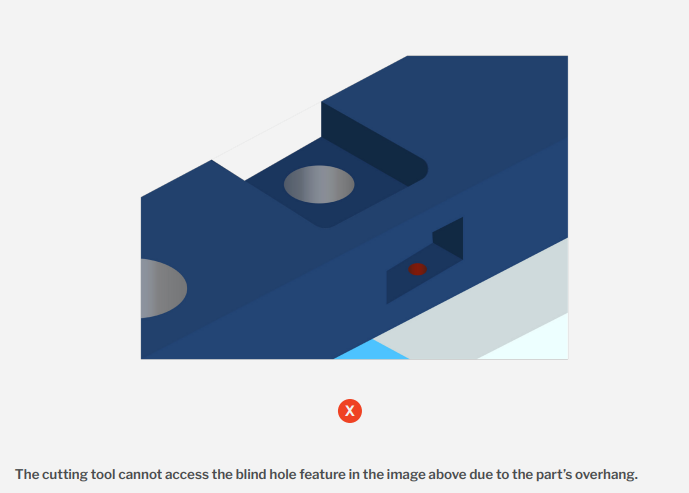
CNC machines perform cutting operations by positioning the cutting tools above the workpiece and applying them downward, this makes it difficult for features hidden from the top angle to be machined. The only exception to this are undercuts which use a cutting tool which can cut cavities horizontally.
Thus it is important to ensure a cutting tool is able to access to all features within a part without being blocked while designing your part to prevent going back to the drawing board!
7. Tolerances
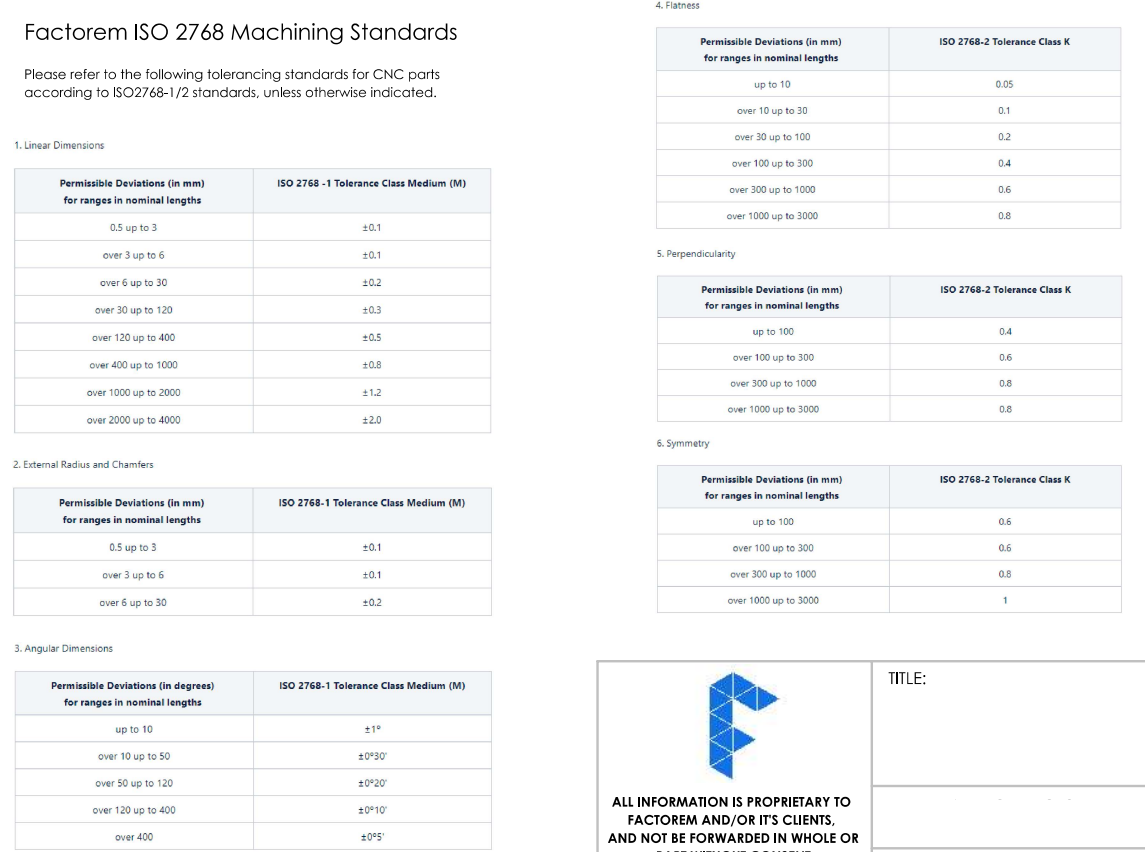
Tolerances are measurements signifying the level/variation of precision needed for your part. CNC machines are capable of achieving very high levels of accuracy, as high as 0.002mm. But such precision requires more machining time, increasing the cost of your part.
Hence, if precision isn't absolutely essential for your part, stick to general tolerances such as Factorem’s ISO 2768 wherever possible to avoid unnecessarily driving up your part’s costs.
8. How Design Choices Impact Production Speed and Cost
As highlighted in the DFM rules above, your design choices have a direct and significant impact on both the speed and cost of CNC manufacturing:
- Increased Machining Time: Features like deep pockets, narrow and deep slots, sharp internal corners (requiring alternative methods), thin walls (requiring slower, more careful cuts), and unnecessarily tight tolerances all necessitate longer machining times. More time on the machine directly translates to higher costs.
- Increased Tooling Costs: Designs requiring long, thin tools (for deep or narrow features), specialized tools (for sharp internal corners or complex contours), or experiencing high tool wear (due to difficult materials or aggressive cuts on poorly designed features) will incur higher tooling costs.
- Increased Setup Complexity and Time: Designs requiring multiple setups to access all features (due to inaccessibility or needing to flip the part) increase non-machining time, adding to the overall cost and lead time.
- Higher Scrap Rate: Features prone to vibration (thin walls), tool breakage (deep, narrow features), or difficult to hold tight tolerances on can lead to a higher number of rejected parts, increasing material waste and overall cost.
- Increased Programming Complexity: Highly complex geometries or designs that don't follow DFM principles often require more complex CAM programming, increasing the time and cost before machining even begins.
9. Tips for Optimizing Complex Geometries
While the DFM rules provide a foundation, optimizing complex geometries requires applying these principles thoughtfully:
- Break Down Complex Features: Can a complex feature be broken down into simpler elements that are easier to machine?
- Standardize Internal Radii: Use a consistent, reasonably large internal radius throughout your design whenever possible. This allows for the use of fewer tools and simpler toolpaths. The radius should be at least slightly larger than the radius of the end mill that will be used.
- Consider 3+2 Axis Machining: For parts with features on multiple faces, a 3+2 axis machine (which can orient the part to a fixed angle and then perform 3-axis machining) can be more cost-effective than full 5-axis simultaneous machining if continuous contours are not required. Ensure features are accessible from a limited number of orientations.
- Evaluate Material Choice: For complex parts, the machinability of the material becomes even more critical. A material that is easier to machine can significantly reduce the time and cost associated with complex geometries.
- Communicate with Your Manufacturer: Share your design intent and any critical features with your manufacturing partner early in the design process. They can provide valuable feedback on manufacturability and suggest optimizations.
Conclusion
Applying these DFM guidelines in your design process will allow you to fully utilize CNC machining’s unique abilities and avoid possible hiccups, all while maximizing your component’s cost efficiency and ensuring high-quality results. While these guidelines provide a great starting point, they are not exhaustive. Each CNC machining project is unique and may require additional considerations based on its specific requirements. Therefore, continuous learning and adaptation are key to mastering the art of CNC machining design.
Successfully implementing DFM requires experience and a deep understanding of the CNC machining process. This is where an on-demand manufacturing platform like Factorem becomes invaluable. Their expertise in DFM ensures that your designs are reviewed and optimized for cost-effectiveness and manufacturability before production begins, saving you time, money, and potential headaches. By working with Factorem, you can leverage their collective knowledge to refine your designs and achieve high-quality parts efficiently.
Ready to ensure your CNC designs are optimized for quality and cost? Partner with Factorem and benefit from expert DFM review and access to a skilled manufacturing network. Get an instant quote today and take the first step towards manufacturing your parts with confidence.
Dive into the complete CNC Machining Content Hub.
References/sources: https://www.fastradius.com/wp-content/uploads/2021/04/CNC-Machining-DFM-Checklist.pdf