The powder coating process was developed in the late 1940s and grew in popularity in the ensuing decades. A powder-coated surface is a hard, plastic-like coating on a metallic surface. The coating itself is made of a polymer that is mixed with pigments. Theses polymers and pigments are heat treated and then crushed to make the necessary powders that are then sprayed onto the part.
Powder Coating Process
Once the powder is prepared, the part undergoes a 3-step process to be powder coated:
1. Metal Preparation
Stainless steel is fed into a pickling solution which serves 2 main purposes. Firstly, the pickling solution removes excess oil, rust and other oxide layers formed on the surface of the steel items. Repeated addition of pickling accelerator increases the lifespan of the stainless steel. Secondly, pickling increasing surface roughness of the stainless steel to increase its adsorption capacity. This will allow the powder to bind more strongly to the metallic surface.
2. Coating
Electrostatic attraction is used by applying a positive charge to the powder in the spray gun and applying a negative charge on the material to be coated. This electrostatic adsorption process produces an evenly coated surface on the workpiece
3. Heat Treatment
Once the coating is applied, the workpiece is then transferred into a baking oven between 180 to 200 degrees Celsius for approximately 15 minutes. This is done to melt, the powder layer and cure it to attain the desired surface quality. After the specified amount of time, the workpiece can be removed from the oven, and it is ready to be used.
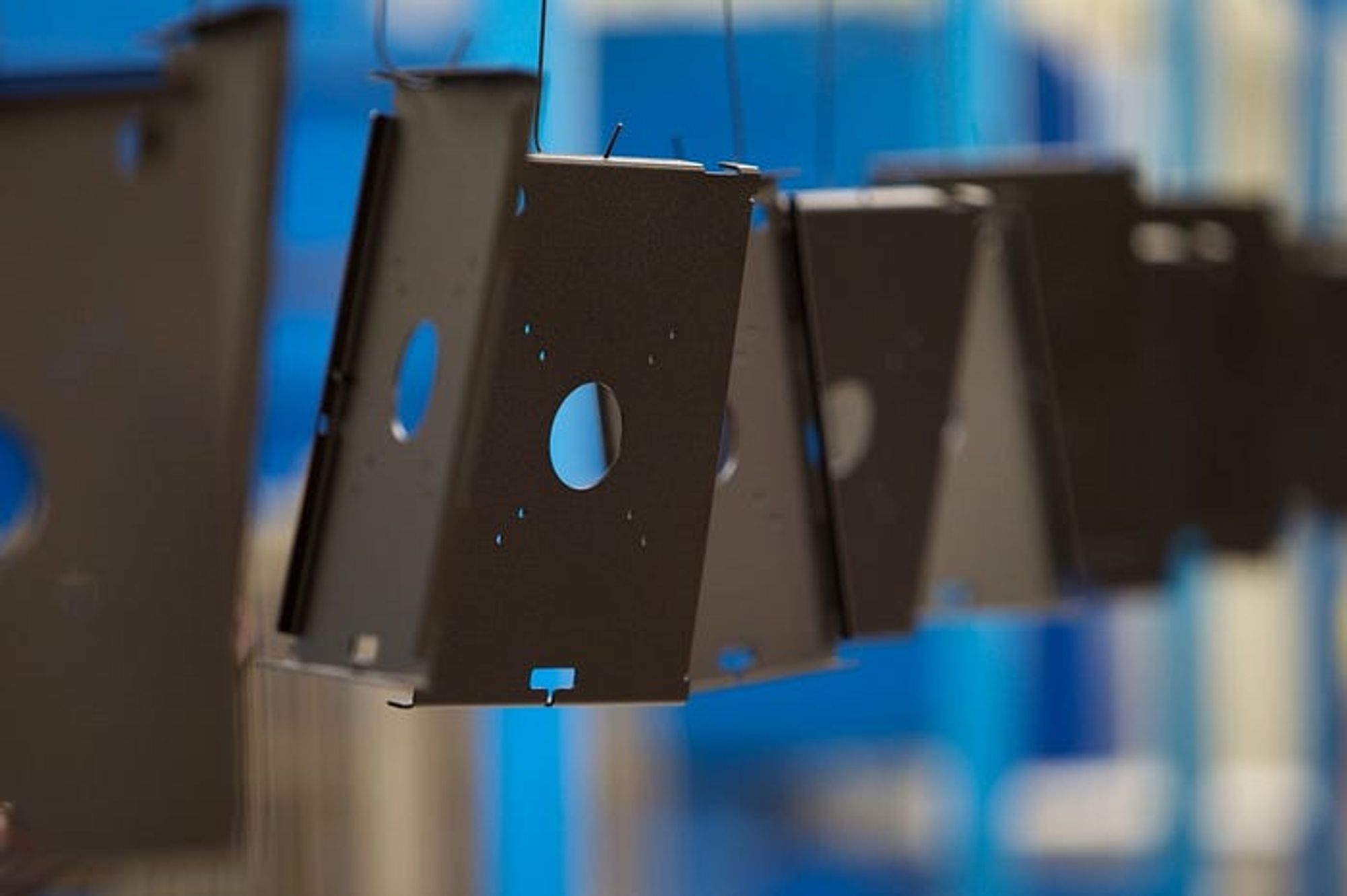
Benefits of Powder Coating
Whilst stainless steel features a naturally shiny surface and is corrosion resistant, engineers and designers still opt to have their parts powder coated. Here are 3 reasons why:
1. Improved Appearance
Powder coating is available in plenty of colours graded on various charts such as the RAL chart, Munsell colour chart, etc. This can be done with various patterns and textures as well which vastly improves the overall finish of the product. It enables engineers to curate a part customised to their liking and at the same time improving the longevity of the stainless steel.
2. Increased Durability
Whilst stainless steel happens to be naturally corrosion resistant, it is not corrosion-proof. This means that stainless steel parts exposed to harsh weather and usage conditions will undergo significant damage. Powder coating helps stainless steel parts stand up to wear and tear caused by weather and other factors, as it is highly resistant to scratching, flaking and corrosion. It can help prevent corrosion of the steel part and extend the life of components used outdoors, underwater or in a working environment.
3. Environmentally Friendly
Powder coating is more environmentally friendly as compared to standard liquid painting of stainless steel. Liquid finishing products typically incorporate certain chemicals that may emit harmful vapours causing damage to the environment as well as to human health with long exposure. Powder coating on the other hand avoids these mishaps by providing a cleaner alternative at little to no additional cost.
At Factorem, we are fortunate to partner with the best surface finishing houses in Singapore to meet all your surface finishing requirements. Get in touch with us as we guide you in achieving the best coatings and surface finish for your ideas!
Thank you for reading!